Leak detection methods, detailed steps, and precautions for bioreactors
In the field of biotechnology, fermentation tanks are the core equipment for achieving biotransformation processes, and their performance directly affects production efficiency and product quality.
However, insufficient sealing performance often leads to microbial contamination, which affects the entire fermentation process.
Therefore, a thorough leak check of the fermentation tank is a key step in ensuring smooth production.
Soap liquid method: This is a simple and effective detection method that judges leaks by applying soap liquid on the surface of a pressurized fermentation tank and observing the generation of bubbles. This method can not only locate the leakage point, but also estimate the leakage amount, making it a powerful assistant for on-site detection.
Sound method: relying on the sound generated during gas leakage, this method is simple and economical, especially suitable for areas that are difficult to observe directly. By listening to the size and frequency of the leaked sound, the severity of the leak can be determined.
The preparation work for the soap solution method includes the following aspects:
1. Prepare soap water and tools: Prepare a spray bottle and towel filled with soap water to apply and observe bubbles.
2. Check the pressure of the air filter: Ensure that the pressure of the air filter is within the range of 0.2-0.3MPa to ensure that the fermentation tank can reach the appropriate pressure.
3. Check the interfaces and valves: Ensure that all interfaces of the fermentation tank are connected properly, the valves and joints are in good condition, and there are no obvious signs of damage or leakage.
4. Close all valves: Before starting the leak check, close all valves to ensure that the fermentation tank is in a closed state.
5. Prepare for intake pressure increase: Slowly open the intake valve and introduce gas into the fermentation tank to prepare for leak detection.
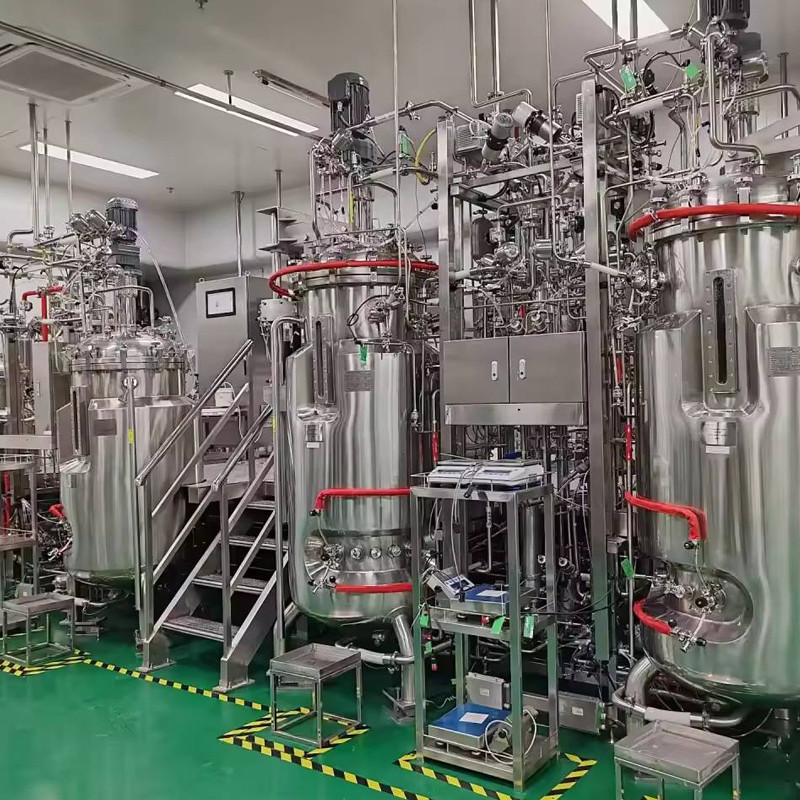
6. Tank body ventilation and pressure maintenance: Slowly increase the pressure inside the fermentation tank to 0.15 MPa and maintain it for 15 minutes, observe the rate of decrease in tank pressure to determine if there is any obvious leakage.
7. Special attention to areas: During the leak detection process, special attention should be paid to valve cores and connections, flange connections, weld joints, and mechanical seals that are prone to leakage.
8. Leakage point inspection: When determining the leakage point, all interfaces should be inspected to ensure that there are no omissions.
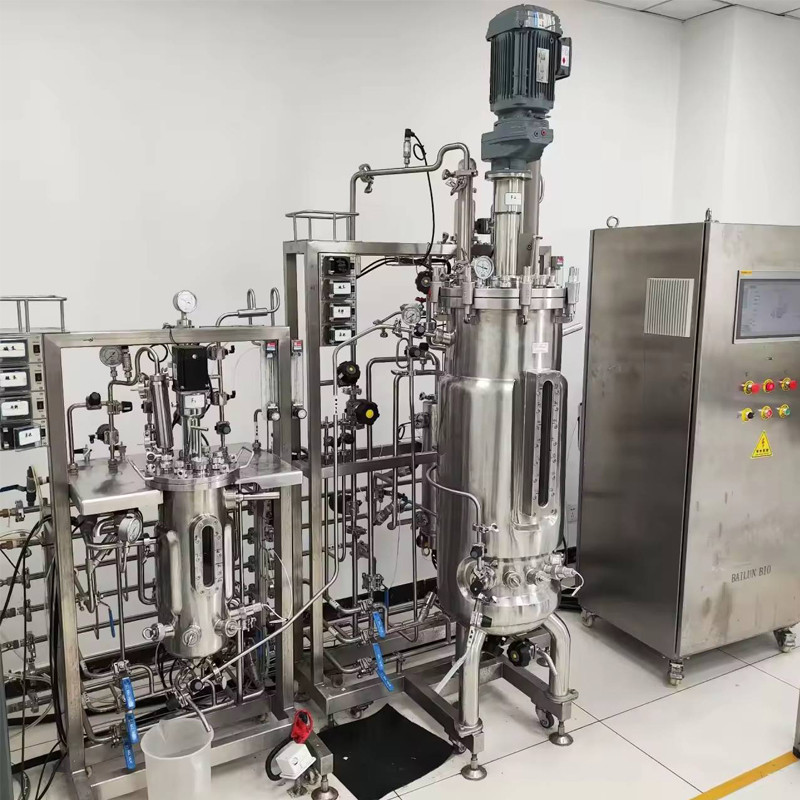
In the process of leak detection, evaluating the degree of leakage by observing the size, number, speed, and duration of bubbles is an intuitive method.
It is also important to observe the location where bubbles appear, as certain areas such as welds, flange connections, valves, etc. may be more prone to leakage.
The sound method is a traditional leak detection method that relies on human hearing to determine the presence of gas leaks.
Although the sound method is a relatively simple leak detection method, it relies on the operator's experience and auditory sensitivity, and therefore serves as a supplement to the soap solution method in practical applications.
