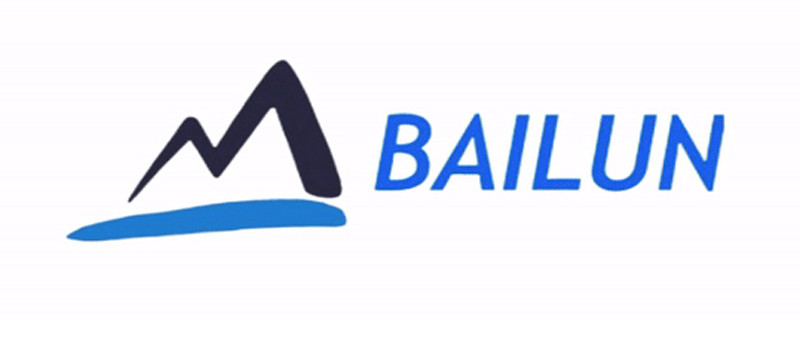
Bailun Biotechnology has established a platform and laboratory for the validation of synthetic biology processes in Songjiang. We welcome discussions, visits, and cooperation.
1、 Clarify the platform's goals and positioning, determine the application areas, and specify which synthetic biology products or processes the platform mainly serves for validation, such as biopharmaceuticals, biochemistry, biomaterials, agricultural biotechnology, and other fields.
The requirements and priorities for process validation vary in different fields, for example, biopharmaceuticals may place more emphasis on product purity, activity, and safety.
Define the validation scale to determine the process validation scale that the platform will cover, including laboratory small-scale testing, pilot scale testing, and possible industrial simulation scale.
The small-scale trial stage is mainly used to preliminarily verify the feasibility of the process and optimize key parameters, while the pilot scale is used to further investigate the stability and repeatability of the process under close to actual production conditions.
The industrial simulation scale helps to discover and solve potential problems in large-scale production in advance.
2、 Infrastructure construction laboratory space layout: Plan specialized laboratory areas, including cultivation rooms, fermentation rooms, purification rooms, analysis and testing rooms, biosafety protection areas, etc.
Ensure that the layout of each functional area is reasonable, meets the requirements of the process flow, facilitates personnel operation and material flow, while considering biological safety and preventing cross contamination factors.
3、 Equipment configuration, installation, and debugging of cell culture and fermentation equipment: Based on the platform positioning and validation scale, suitable bioreactors are configured, such as stirred bioreactors, air lift bioreactors, disposable bioreactors, etc., with precise control functions for temperature, pH, dissolved oxygen, stirring speed, etc., to meet the needs of different types of microorganisms or cell cultures.
At the same time, equipped with corresponding seed cultivation equipment, culture medium preparation equipment, sterilization equipment, etc.
Purification equipment: equipment installed for product separation and purification, such as centrifuges, filtration equipment (including microfiltration, ultrafiltration, nanofiltration, etc.), chromatography systems (ion exchange chromatography, affinity chromatography, gel filtration chromatography, etc.), freeze-drying machines, etc.
Ensure that the performance of these devices meets product purity and quality requirements, and has good stability and reliability.
Analytical testing instruments: equipped with a series of high-precision analytical testing instruments, used for quality monitoring and analysis of raw materials, intermediate products, and final products.
Environmental monitoring and control system: Establish a comprehensive environmental monitoring system to monitor and control real-time environmental parameters such as temperature, humidity, cleanliness, and pressure in the laboratory.
Install an air purification system to ensure that the air quality in the laboratory meets the corresponding standard requirements, and prevent microbial contamination and dust particles from affecting the experimental results.
4、 Establishment of Technical Platform and Experimental Design (DoE) Method: Using statistical experimental design principles such as orthogonal design, response surface design, etc., systematically study the impact of multiple process parameters on product quality and yield, screen key process parameters, and establish mathematical models to predict process performance, thereby achieving process optimization design.
By using the DoE method, the number of experiments can be reduced, experimental efficiency can be improved, and more comprehensive and accurate process information can be obtained.
Application of Process Analysis Technology (PAT): Introducing PAT tools such as online spectroscopic analysis (near-infrared spectroscopy, Raman spectroscopy, etc.), online biosensors (glucose sensors, lactate sensors, dissolved oxygen sensors, etc.), and process imaging technology (particle imaging analysis, fluorescence imaging, etc.) to achieve real-time monitoring and control of key process steps such as fermentation and purification processes.
For example, by monitoring the dissolved oxygen level and pH value changes during the fermentation process online, the aeration rate and acid-base addition can be adjusted in real time to maintain the optimal environmental conditions for microbial growth.
Establish quality standards and testing methods: Based on relevant regulations and industry standards, combined with product characteristics, develop comprehensive quality standards for raw materials, intermediate products, and final products.
Establish corresponding analysis and detection methods, including qualitative and quantitative analysis methods, and conduct methodological validation on these methods to ensure their accuracy, repeatability, specificity, and sensitivity.