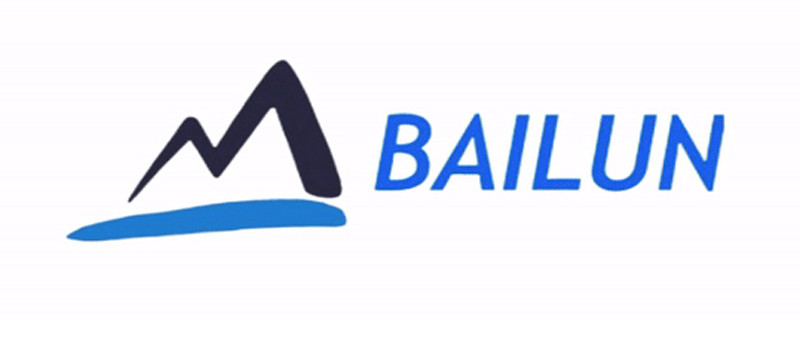
Foam is a colloidal system in which gas is dispersed in a small amount of liquid. The foam is separated by a liquid film and is not connected with each other. The dispersed phase of foam encountered during fermentation is sterile air and metabolic gas, and the continuous phase is fermentation broth.
1、 Type of foam
A type that exists on the liquid surface of fermentation broth. This type of foam has a large proportion of gas phase, and there is a braided boundary between the foam and the liquid below it. As seen in some thin pre fermentation or seed culture media.
Another kind of foam is found in the thick mycelium fermentation liquid. This foam is finely dispersed, even and stable. There is no obvious wave boundary between foam and liquid, and the proportion of gas dispersed phase in bubbling fermentation broth gradually increases from bottom to top.
2、 Causes of foam formation during fermentation
1. The intensity of aeration and agitation is high. The strong aeration and agitation can increase the foam. Therefore, in the early stage of fermentation, the nutrient consumption of the culture medium is low, and the culture medium is rich in components, which is easy to foam. The ventilation volume should be reduced first, and then gradually increased. The stirring speed is also the same. Defoamers can also be added to the base material.
2. The ratio of the culture medium and the composition of raw materials The culture medium is rich in nutrition, high in viscosity, and produces many and lasting foam. It is difficult to start mixing in the early stage.
3. The quality of strain, seed and inoculation amount is good, the growth rate is fast, the soluble nitrogen source is used quickly, and the probability of foam production is less. For strains with slow growth, the inoculation amount can be increased.
4. Sterilization quality The sterilization quality of the culture medium is poor, sugar and nitrogen are destroyed, inhibiting the growth of microorganisms, making the seed hyphae self dissolve, producing a lot of foam, and adding defoamer is also ineffective.
3、 Effect of foam on fermentation
The utilization rate of fermentation equipment is reduced, the heterogeneity of the flora is increased, the chance of contamination is increased, the loss of products is caused, and the defoamer will bring difficulties to the subsequent extraction process. The metabolic gas in the foam is not easy to be taken away, changing the living environment, causing abnormal metabolism of the cell, leading to early autolysis of the cell.
4、 Detection and control of foam in fermentation process
The simplest detection method is to regularly observe the foam generation on the sight hole of the fermentation tank. When foam continues to rise, open the valve of the defoamer storage tank and add a small amount of defoamer to make the foam disappear.
A liquid level gauge can also be installed at the top of the tank and connected to the control instrument to control the opening of the defoaming storage rate valve. The signal generated when the foam rises to contact the top of the probe will be commanded to open the pump switch or valve through the control device, and the defoamer will be automatically added. When the foam disappears, the signal will also disappear, and the valve will be closed. Control method: Physical defoaming method.
Chemical defoaming method reduces the components that are prone to foaming in the culture medium, reduces the components with high viscosity in the culture medium, and appropriately reduces the ventilation rate and stirring speed.
Principle of physical defoaming method: use mechanical force to cause strong vibration or pressure change to cause foam to burst, or use mechanical force to separate and recover the liquid in the discharged gas. Method: The simplest method for foam removal in the tank is to install foam removal slurry on the upper part of the mixing shaft.
The method of defoaming outside the tank is to lead the foam out of the tank and return the liquid to the tank after defoaming. Advantages: No need to introduce external substances, save raw materials, and reduce pollution opportunities. Disadvantages: The factors causing stable foam cannot be eliminated from the general public.