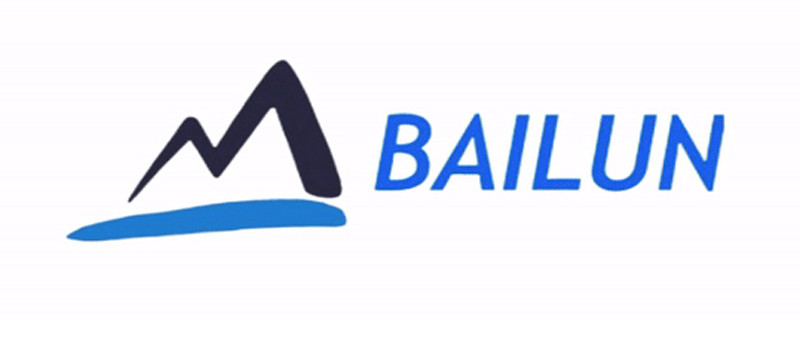
In the process of modern industrial automation, industrial control systems (ICS) play a crucial role, with SCADA, DCS, and PLC being important components but easily confused.
SCADA system features: As a data acquisition and monitoring system, it integrates data acquisition, transmission, and human-machine interface (HMI) software. Its main function is to collect on-site information, such as various sensor data along remote oil and gas pipelines, and then transmit this data to a computer system to present it to operators in intuitive image or text form.
Operators can monitor the entire system in real-time from a centralized location and automatically perform operations such as opening and closing valves, adjusting equipment parameters, etc.
Application scenarios: Especially suitable for monitoring equipment distributed throughout cities such as water treatment plants, remote management of long-distance oil and gas pipeline transportation, real-time monitoring of substations and lines in power transmission and distribution systems, and remote control of various facilities along railways that require monitoring across large geographical areas.
DCS system functional characteristics: Distributed control system is mainly used for production process control in the same geographical location environment. It enables local controllers to work collaboratively through centralized monitoring, effectively executing the entire production process.
For example, in a refinery, the controllers of different reaction vessels, distillation towers, and other equipment operate accurately under the coordination of the DCS system, reducing the impact of individual equipment failures on the entire production system.
At the same time, it has interfaces with enterprise systems, which can integrate various data and states of the production process into the overall business operation of the enterprise. This not only improves production efficiency, but also gives production higher flexibility and scalability. Enterprises can adjust production processes and parameters more conveniently according to business needs.
Application scenarios: It is a common control system in industrial control fields such as oil refining, sewage treatment plants, power plants, chemical plants, and pharmaceutical plants. In sewage treatment plants, the DCS system can adjust the equipment operating parameters of each treatment stage in real time based on water quality monitoring data to ensure that the sewage treatment effect meets the standards.
PLC system functional characteristics: Programmable logic controller is a new industrial control device that integrates microelectronics, computers, automatic control, and communication technologies on the basis of traditional sequential controllers. Its purpose is to replace traditional relays, achieve sequential control functions such as logic operation, timing, and counting, and build a flexible programmable control system.
It has user programmable memory that can store instructions for specific functions such as input/output (I/O) control (such as controlling motor start and stop, sensor signal acquisition, etc.), logical judgment (performing different operations based on different conditions), timed tasks (such as timed start or stop of a device), counting operations (counting product quantity, etc.), PID control (accurately adjusting temperature, pressure and other parameters), communication functions (exchanging data with other devices or systems), arithmetic operations (calculating production data), data and file processing, etc.
In the industrial automation and control system network system, PLC, as a key control component, directly acts on the specific operation and process control of industrial equipment.
Application scenarios: Widely used in various industrial production scenarios, such as robotic arm control in automated production lines, action coordination of packaging equipment, tool switching of processing equipment, etc. It also plays an indispensable role in SCADA and DCS systems.
The relationship between SCADA, DCS, and PLC in industrial control systems is both distinct and interconnected.
Conceptually, SCADA and DCS belong to the system level concepts, while PLC is the specific control device.
In terms of application requirements, DCS focuses on process automation, such as controlling complex chemical reactions in chemical production processes; PLC focuses on the production line process of factory automation, such as controlling the equipment actions at various workstations on the automotive assembly line; SCADA is designed to meet the monitoring requirements of wide area systems.
From the perspective of computers and networks, there is a hierarchical relationship between them. SCADA is equivalent to the scheduling management layer, responsible for overall scheduling and monitoring; DCS is the management layer of the factory station, which manages the production process of various stations or workshops within the factory; PLC is located at the field equipment layer, directly controlling various industrial equipment on site.
With the development of technology, the boundaries between the three are gradually blurred, and their integration and collaborative work have become increasingly important, jointly promoting the continuous development of industrial automation to meet the growing demand for industrial production, improve production efficiency, ensure production safety and product quality.