The Automatic Fermenter Bioreactor: Unleashing Potential in 100L Fermentation for Bacteria Cultivation
In the ever-evolving landscape of biotechnology and microbiology, the Automatic Fermenter Bioreactor, especially in the 100L capacity range, has emerged as a powerful tool with the potential to transform various industries and research endeavors. This article aims to provide an in-depth exploration of this remarkable technology, covering its design, functionality, applications, and the significant impact it has on bacterial fermentation processes.
The design of the Automatic Fermenter Bioreactor 100L is a harmonious blend of mechanical, electrical, and biochemical engineering principles. The bioreactor vessel is constructed from materials that offer durability, chemical resistance, and sterilization compatibility. Stainless steel, with its superior properties, is often the material of choice, ensuring a hygienic and long-lasting containment for the fermentation process.
The inner workings of the bioreactor are meticulously engineered. The agitation system is designed to provide gentle yet effective mixing, ensuring uniform distribution of nutrients, oxygen, and heat throughout the 100L volume. Different types of agitators, such as Rushton turbines or pitched blade impellers, are selected based on the specific requirements of the bacterial culture and the viscosity of the medium.
Temperature control is a critical aspect of the design. The bioreactor is equipped with heating and cooling jackets or coils that can precisely regulate the internal temperature. This is essential as bacteria have specific temperature optima for growth and metabolism, and deviations can significantly affect the fermentation outcome.
The aeration system is another crucial component. It is responsible for delivering the right amount of oxygen to support the respiratory needs of the bacteria. Specialized spargers or membrane aerators are employed to ensure efficient gas transfer without causing excessive foaming or damaging the cells.
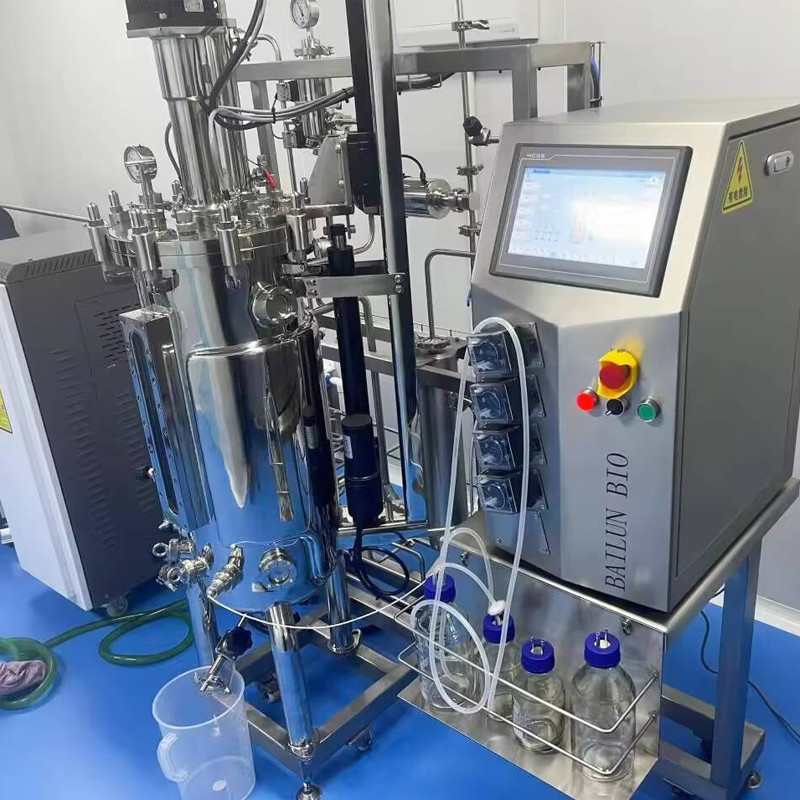
The automatic control system is the brain of the Automatic Fermenter Bioreactor 100L. It integrates sensors that continuously monitor parameters such as pH, dissolved oxygen levels, cell density, and substrate concentration. Based on the data collected, the control system makes real-time adjustments to factors like agitation speed, aeration rate, and nutrient addition to maintain the optimal conditions for bacterial growth and product formation.
The functionality of this bioreactor is truly remarkable. It offers a highly controlled and reproducible environment for bacterial cultures. The ability to precisely adjust and maintain parameters allows for consistent and efficient fermentation processes. This is particularly important in industrial settings where large-scale production demands uniformity and reliability.
One of the key advantages of the 100L capacity is its scalability. It serves as an intermediate step between small-scale laboratory experiments and large industrial-scale fermentations. Researchers and producers can optimize the process at this scale before moving on to even larger operations, reducing the risks and uncertainties associated with scale-up.
The applications of the Automatic Fermenter Bioreactor 100L are wide-ranging and diverse. In the pharmaceutical industry, it is used for the production of antibiotics, enzymes, and therapeutic proteins. The controlled conditions enable the bacteria to express the desired genes and produce high-quality, pure compounds that meet strict regulatory standards.
In the food and beverage sector, it plays a vital role in the production of fermented foods like yogurt, cheese, and alcoholic beverages. The precise control over the fermentation process ensures consistent flavor, texture, and quality of the final products.
The bioreactor also finds application in the field of environmental biotechnology. Bacteria can be cultivated in it to degrade organic pollutants or produce biofuels, contributing to sustainable solutions for environmental challenges.
In the realm of research, it provides a platform for scientists to study the metabolic pathways of bacteria, investigate the effects of different conditions on bacterial growth and product formation, and develop novel fermentation strategies.
However, operating an Automatic Fermenter Bioreactor 100L is not without its challenges. Maintaining sterility throughout the process is of utmost importance. Any contamination can lead to batch failure and significant economic losses. Regular cleaning and sterilization procedures must be rigorously followed, and the integrity of the seals and connections must be constantly checked.
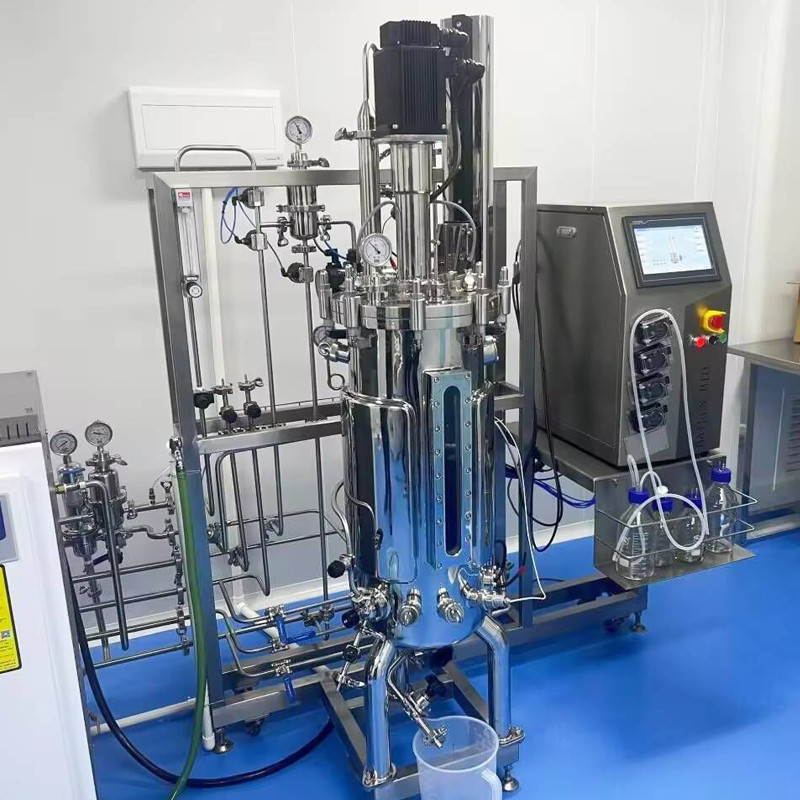
Calibration and validation of the sensors and control systems are essential to ensure the accuracy and reliability of the data and the resulting control actions. Additionally, optimizing the fermentation process for different bacterial strains and products often requires a deep understanding of microbiology and process engineering, as well as extensive experimentation.
Despite these challenges, the benefits offered by the Automatic Fermenter Bioreactor 100L far outweigh the difficulties. Ongoing technological advancements are addressing these issues, making the operation and maintenance of these bioreactors more straightforward and efficient.
In conclusion, the Automatic Fermenter Bioreactor 100L stands as a testament to human ingenuity in the field of biotechnology. Its ability to provide a controlled, scalable, and efficient environment for bacterial fermentation has opened up new possibilities in various industries and research areas. As we continue to explore and innovate, this technology is likely to play an even more crucial role in shaping the future of microbiology and related fields.