The 10L Fermentor, Minifor Glass Fermenter, and Laboratory Bioreactor: Unleashing Potential in Research and Innovation
In the realm of scientific research and biotechnological advancements, the 10L fermentor, Minifor glass fermenter, and laboratory bioreactor have emerged as essential tools that hold the key to unlocking new possibilities and driving innovation. This article explores the intricate details, functionality, applications, and the significant impact these devices have on various fields of study.
The 10L fermentor represents a significant capacity that strikes a balance between providing sufficient volume for meaningful experiments and remaining manageable within a laboratory setting. This size is often chosen for its ability to generate substantial amounts of product or biomass while allowing for close monitoring and control of the fermentation process. The design of the 10L fermentor is engineered to optimize various parameters crucial for successful fermentation.
One of the key features of a 10L fermentor is its precise control over environmental conditions. Temperature regulation is of utmost importance as it directly influences the metabolic rates and enzymatic activities of the organisms.
Sophisticated heating and cooling systems ensure that the internal temperature remains stable and within the optimal range for the specific organisms or processes being studied. pH control is another critical aspect, as even slight deviations can have a significant impact on the growth and productivity of the cultures. Automated pH adjustment systems maintain the pH at the desired level, creating an environment conducive to efficient fermentation.
Aeration and agitation play vital roles in the 10L fermentor. Adequate oxygen supply is essential for aerobic organisms, and the agitation system ensures uniform distribution of oxygen and nutrients throughout the vessel. This promotes homogeneity and prevents the formation of gradients that could negatively affect the fermentation process. The design and speed of the agitation mechanism can be tailored to the specific requirements of the organisms and the nature of the substrate being fermented.
The Minifor glass bioreactor fermenter offers unique advantages due to its construction material. The transparency of glass allows for direct visual inspection of the fermentation process. Researchers can observe the growth, morphology, and behavior of the microorganisms or cells in real-time, providing valuable insights that may not be obtainable through indirect measurement methods alone. This visual access is particularly useful for identifying any abnormalities or changes in the culture and enables prompt corrective actions.
The glass surface also provides a chemically inert environment, minimizing the risk of interactions or contamination that could potentially affect the integrity of the fermentation. Moreover, the Minifor glass fermenter is often designed with modular components, allowing for easy customization and adaptation to specific experimental needs.
It can be equipped with various sensors and probes to monitor parameters such as dissolved oxygen, redox potential, and biomass concentration, providing a comprehensive understanding of the fermentation dynamics.
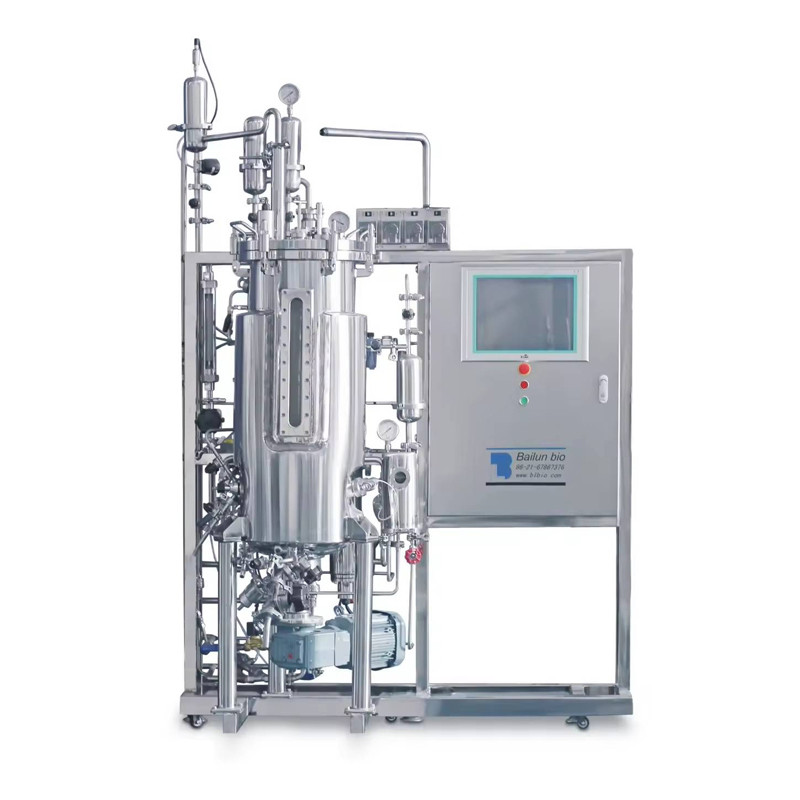
The laboratory bioreactor serves as a versatile platform for a wide range of applications. In the field of microbiology, it is used for the cultivation and study of various microorganisms, including bacteria, yeast, and fungi. Researchers can investigate their metabolic pathways, growth kinetics, and the production of secondary metabolites. This knowledge is crucial for the development of antibiotics, enzymes, and other bioactive compounds.
In the realm of cell culture, the laboratory bioreactor provides an optimal environment for the growth and differentiation of mammalian cells. It is essential for the production of therapeutic proteins, vaccines, and cell-based therapies. The controlled conditions within the bioreactor support the complex needs of these cells, ensuring their viability and functionality.
The food and beverage industry also benefits from these laboratory-scale devices. They are used for the development and optimization of fermentation processes for the production of beverages, dairy products, and fermented foods. The ability to precisely control the fermentation parameters results in consistent quality, flavor, and texture of the final products.
Pharmaceutical research heavily relies on the laboratory bioreactor for early-stage drug discovery and development. It allows for the evaluation of drug candidates on cellular models, providing valuable data on efficacy and toxicity. The bioreactor also enables the optimization of drug delivery systems and the study of drug metabolism and interactions within a cellular context.
However, working with these devices comes with its own set of challenges. Maintaining aseptic conditions is of paramount importance to prevent contamination, which can lead to failed experiments and compromised results. The calibration and validation of sensors and control systems are essential to ensure the accuracy and reliability of the data collected. Additionally, the operation and maintenance of these devices require a certain level of technical expertise and adherence to strict protocols.
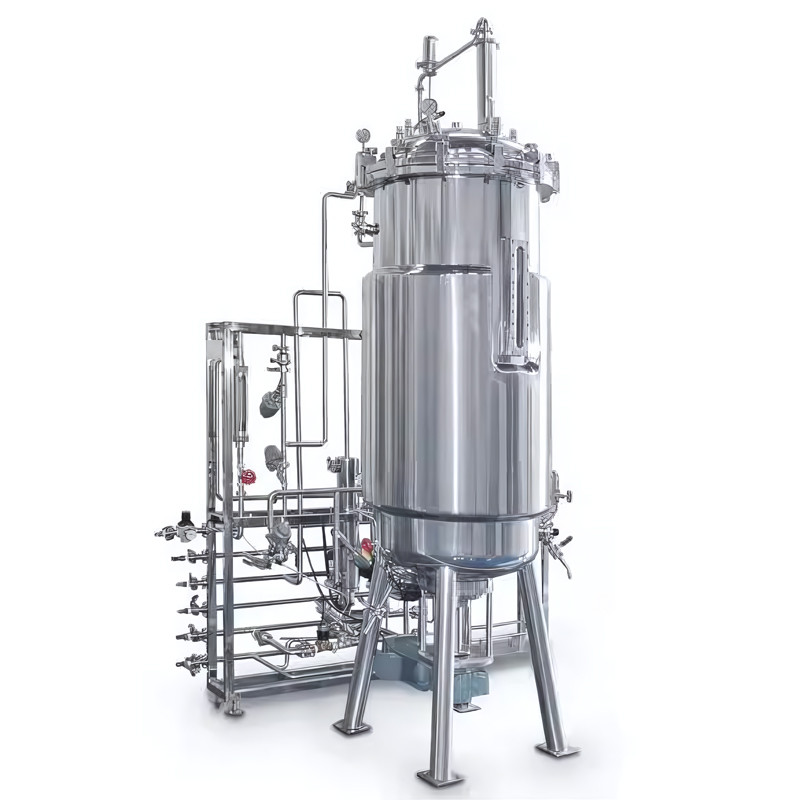
Looking towards the future, advancements in technology are expected to further enhance the capabilities of the 10L fermentor, Minifor glass fermenter, and laboratory bioreactor. The integration of artificial intelligence and machine learning algorithms will enable predictive modeling and real-time optimization of the fermentation process. New materials and coatings will improve the durability and performance of the vessels, while miniaturization and portability will expand their application in point-of-care and field-based research.
In conclusion, the 10L fermentor, Minifor glass fermenter, and laboratory bioreactor are not just tools but powerful enablers in the pursuit of scientific knowledge and technological progress. Their ability to provide controlled, observable, and scalable environments for biological processes has opened up new frontiers in various fields, and their continued evolution will undoubtedly shape the future of biotechnology and related industries.