Lab Fermentation Bioreactor For Bacteria: Unveiling the Secrets of Microbial Growth and Production
In the realm of microbiology and biotechnology, the lab fermentation bioreactor for bacteria plays a crucial role in understanding and manipulating the growth and metabolic processes of these microscopic organisms. This article aims to provide an in-depth exploration of these bioreactors, highlighting their design, functionality, applications, and the challenges they present.
The design of a lab fermentation bioreactor for bacteria is a meticulous combination of engineering and biological principles. The bioreactor typically consists of a vessel made of materials that are resistant to chemical corrosion and can withstand sterilization processes to maintain a sterile environment. The size and shape of the vessel are determined based on the scale of the experiments and the volume of culture required.
One of the key components of the bioreactor is the agitation system. This ensures uniform mixing of the culture medium, preventing the formation of gradients in nutrients, oxygen, and pH. Different types of agitators, such as impellers or magnetic stirrers, are used depending on the viscosity of the medium and the specific requirements of the bacterial culture.
Temperature control is another essential aspect. The bioreactor is equipped with heating or cooling jackets or coils to maintain the optimal temperature for bacterial growth and metabolism. Precise temperature regulation is crucial as even slight variations can significantly affect the activity of enzymes and the overall physiological state of the bacteria.
Oxygen supply is of paramount importance, especially for aerobic bacteria. Aeration systems, such as spargers or membrane oxygenators, are incorporated to provide the necessary oxygen. The rate of oxygen transfer is carefully controlled to meet the respiratory demands of the bacteria without causing excessive foaming or oxidative stress.
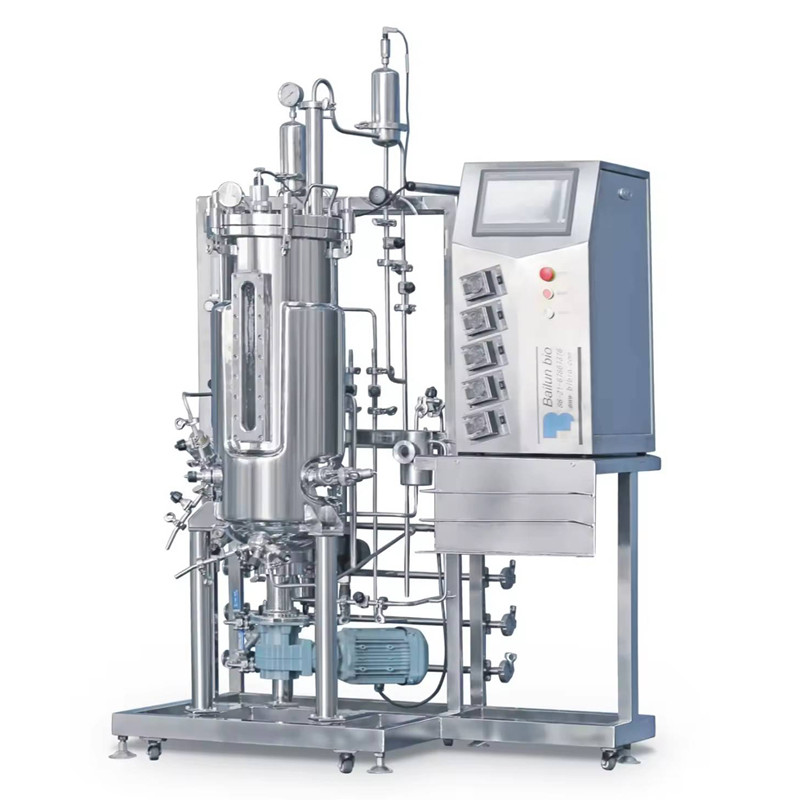
The functionality of the lab fermentation bioreactor lies in its ability to provide a controlled and monitored environment for bacterial cultures. Sensors are installed to measure and monitor various parameters in real-time, including pH, dissolved oxygen levels, cell density, and metabolite concentrations. This data is crucial for understanding the kinetics of bacterial growth and metabolism and for making timely adjustments to optimize the process.
The applications of these bioreactors are vast and diverse. In the field of medicine, they are used for the production of antibiotics, vaccines, and therapeutic proteins. By manipulating the growth conditions and genetic makeup of bacteria, researchers can engineer these microorganisms to produce valuable drugs and biomolecules.
In the food industry, lab fermentation bioreactors are employed for the production of fermented foods and beverages, such as yogurt, cheese, and beer. Understanding the growth and metabolic activities of bacteria in these systems helps in developing improved fermentation processes and products with enhanced quality and flavor.
Environmental biotechnology also benefits from these bioreactors. They can be used to study the degradation of pollutants by bacteria and to develop bioremediation strategies for cleaning up contaminated environments.
However, working with lab fermentation bioreactors for bacteria comes with its challenges.
Maintaining sterility throughout the process is of utmost importance to prevent contamination and ensure the validity of the experiments. This requires strict aseptic techniques and regular sterilization of the equipment and medium.
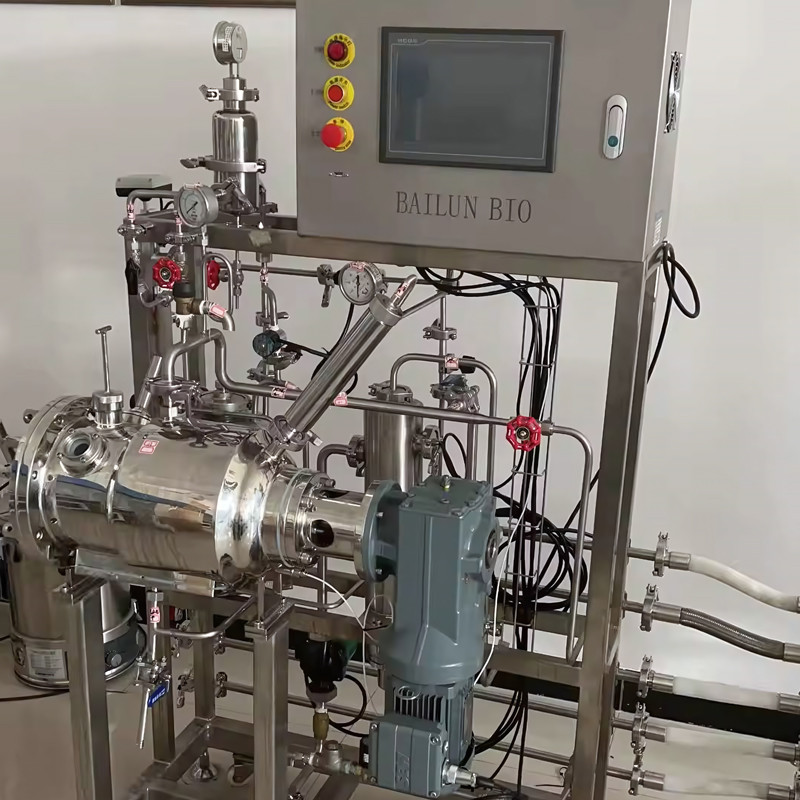
The optimization of process parameters, such as the composition of the culture medium, the agitation speed, and the aeration rate, can be a complex and time-consuming task. It often requires extensive experimentation and the use of statistical design of experiments to determine the optimal conditions for maximum productivity.
Another challenge is the scale-up from the lab scale to industrial production. While the results obtained in the lab provide valuable insights, scaling up the process often introduces new challenges related to mass transfer, heat transfer, and process control that need to be addressed carefully.
In conclusion, the lab Industrial Microbiology fermentation bioreactor for bacteria is an indispensable tool in modern microbiology and biotechnology. Its ability to create a controlled and monitored environment enables researchers to unlock the potential of bacteria for various applications.
Despite the challenges, continuous advancements in technology and research are enhancing the performance and capabilities of these bioreactors, opening up new possibilities for scientific discovery and industrial innovation.