Insights into CIP Stations
In the dynamic and highly regulated world of industrial processes, maintaining the cleanliness and hygiene of filling tanks is of paramount importance. The Clean-in-Place (CIP) station has emerged as a revolutionary solution, ensuring the efficient and thorough cleaning of these essential components of various production lines.
Filling tanks are at the core of numerous industries, from food and beverage to pharmaceuticals and chemicals. They play a crucial role in storing and dispensing products, and any contamination or residue build-up can have serious implications for product quality, safety, and compliance with industry standards. This is where the CIP station comes into play, offering a systematic and automated approach to tank cleaning.
The design of a CIP station for filling tanks is a complex yet carefully engineered process. It typically consists of several key components working in harmony to deliver an effective cleaning cycle. At the heart of the system are storage tanks for holding cleaning solutions, such as detergents, acids, and alkalis, each formulated to target specific types of contaminants. These solutions are precisely metered and mixed to create the ideal cleaning cocktail based on the nature of the tank contents and the level of soiling.
Pumps are another critical element of the CIP station. They generate the necessary pressure and flow rate to ensure that the cleaning fluids reach every nook and cranny of the filling tank. The power and capacity of the pumps are selected to accommodate the size and configuration of the tanks being cleaned, ensuring a vigorous and uniform circulation of the cleaning agents.
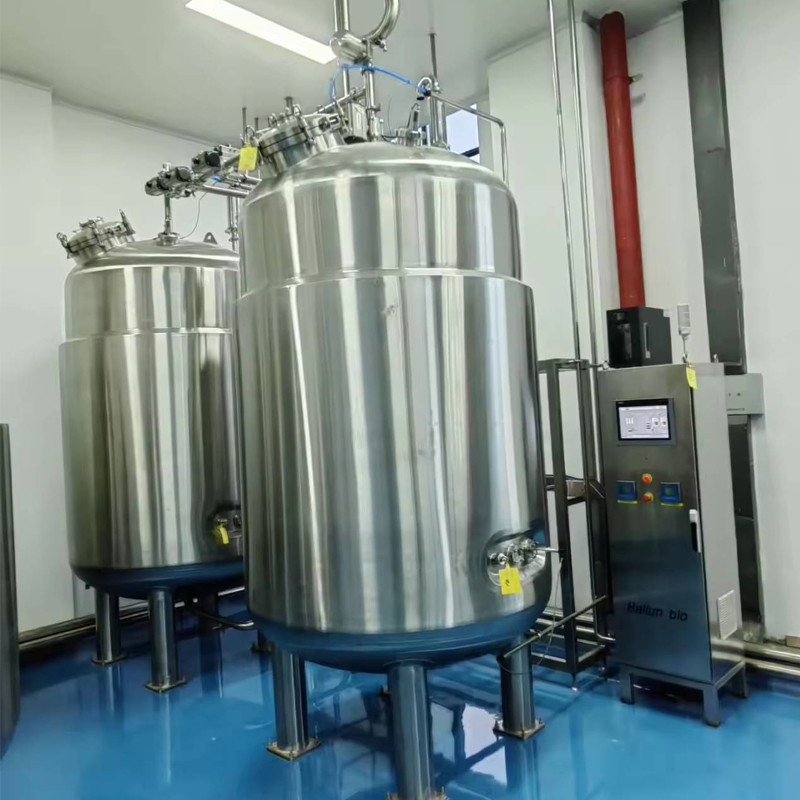
Heating and cooling systems are often integrated into the CIP station to control the temperature of the cleaning fluids. The right temperature can enhance the cleaning action of the solutions, facilitating the removal of stubborn residues and greases. Temperature control is especially crucial in industries where product viscosities and adherence to the tank surfaces can vary significantly.
Valves and piping networks play a vital role in directing the flow of the cleaning fluids. These components are strategically arranged to enable sequential rinsing, cleaning, and sanitizing steps, ensuring that all parts of the filling tank are exposed to the appropriate treatment at the right time. Sophisticated control systems monitor and regulate the opening and closing of these valves, ensuring a precise and repeatable cleaning process.
One of the significant advantages of the CIP cip system station is its ability to automate the cleaning process. This not only reduces the reliance on manual labor but also minimizes human error and ensures consistency in the quality of cleaning. Programmable logic controllers (PLCs) or computer-based control systems allow for the customization of cleaning cycles, based on factors such as the type of product previously stored in the tank, the duration since the last cleaning, and the specific requirements of the production schedule.
In the food and beverage industry, where filling tanks handle a wide range of products with varying viscosities and compositions, the CIP station is indispensable. It helps prevent cross-contamination between different batches and flavors, maintaining the integrity and taste of the final products. For example, in a juice bottling plant, the CIP station ensures that after filling one type of juice, the tanks are thoroughly cleaned before being used for another flavor, preventing any flavor transfer or spoilage.
In the pharmaceutical sector, the stakes are even higher. Filling tanks used for drugs and vaccines must adhere to strict regulatory standards for cleanliness and sterility. The CIP station in this context is designed to provide a highly controlled and validated cleaning process, with detailed documentation of each cleaning cycle to demonstrate compliance. Any residue or microbial contamination could compromise the efficacy and safety of the pharmaceutical products, making the role of the CIP station critical in maintaining quality and patient safety.
The chemical industry also benefits from CIP stations for filling tanks. Here, the cleaning process must address the potential presence of aggressive chemicals and residues that can pose hazards if not properly removed. The CIP station is engineered to handle these challenging substances and ensure that the tanks are safe for subsequent use.
However, operating a CIP station for filling tanks is not without its challenges. The initial investment in the equipment can be substantial, including the cost of the station itself, installation, and integration with existing production lines. Additionally, the selection and management of cleaning solutions require careful consideration to ensure they are effective yet environmentally friendly and compliant with relevant regulations.
Maintenance of the CIP station is also crucial to its long-term performance. Regular checks of pumps, valves, sensors, and control systems are necessary to identify and address any potential issues before they affect the cleaning process. Training of operators is essential to ensure they understand the workings of the system and can troubleshoot any problems that arise.
Looking to the future, the development of CIP stations for filling tanks is likely to be driven by several trends. Advances in sensor technology will enable real-time monitoring of the cleaning process, providing immediate feedback on the effectiveness of the cleaning and allowing for on-the-fly adjustments. The integration of artificial intelligence and machine learning algorithms could optimize the cleaning cycles based on historical data and predictive analytics, further enhancing efficiency and reducing costs.
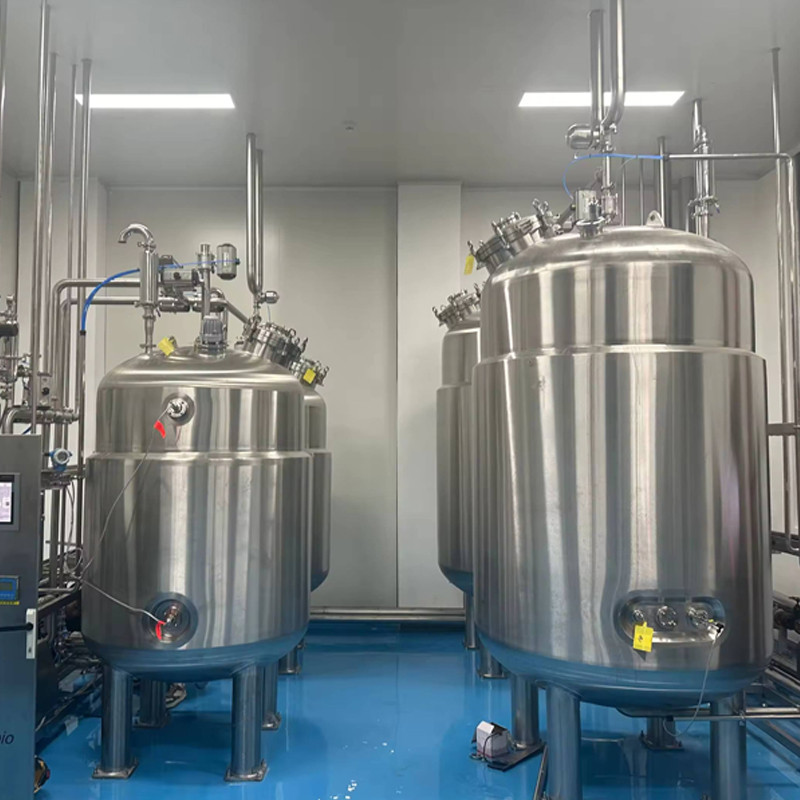
Sustainability will also be a key focus. The development of more eco-friendly cleaning solutions and the optimization of water and energy usage within the CIP station will be important to minimize the environmental impact of the cleaning process.
In conclusion, the CIP station has transformed the way filling tanks are cleaned in various industries. Its ability to provide efficient, automated, and customizable cleaning solutions has become essential for maintaining product quality, operational efficiency, and regulatory compliance. As technology continues to advance and industries' demands for cleanliness and hygiene become more stringent, the role of the CIP station is set to become even more crucial in ensuring the smooth and safe operation of production processes.