Industrial Fermenters and Bioreactors: From Laboratory to Large-Scale Production
In the realm of modern industrial processes and biotechnology, fermenters and bioreactors play a crucial role in the production of a wide range of valuable products. This article explores the world of industrial fermenters and bioreactors, with a particular focus on their application from the laboratory scale to large-scale industrial production.
The laboratory fermentation tank serves as the starting point for many research and development efforts. It provides a controlled environment where scientists can conduct experiments, optimize conditions, and study the behavior of microorganisms or cells. These tanks are typically smaller in size but are equipped with essential monitoring and control systems to maintain precise parameters such as temperature, pH, dissolved oxygen, and agitation.
In the laboratory setting, the flexibility and adaptability of the fermentation tank are highly valued. Researchers can easily modify and test different variables to understand the fundamental aspects of the fermentation process. This initial stage of experimentation is critical for laying the foundation for future scale-up and industrial application.
As research progresses and the process shows promise for commercialization, the transition to industrial-scale fermenters and bioreactors becomes necessary. Industrial fermenters are designed to handle large volumes of substrate and operate continuously for extended periods. They are often constructed with robust materials to withstand the demanding conditions of industrial production.
One of the key challenges in scaling up from the laboratory to industrial scale is maintaining the homogeneity of the culture environment. In a small laboratory tank, it is relatively easier to ensure uniform distribution of nutrients, oxygen, and heat. However, in a large industrial fermenter, achieving this uniformity requires careful design of the agitation and aeration systems.
Advanced impeller designs and optimized gas sparging techniques are employed to prevent the formation of dead zones and ensure that all cells have access to the necessary resources for growth and metabolism.
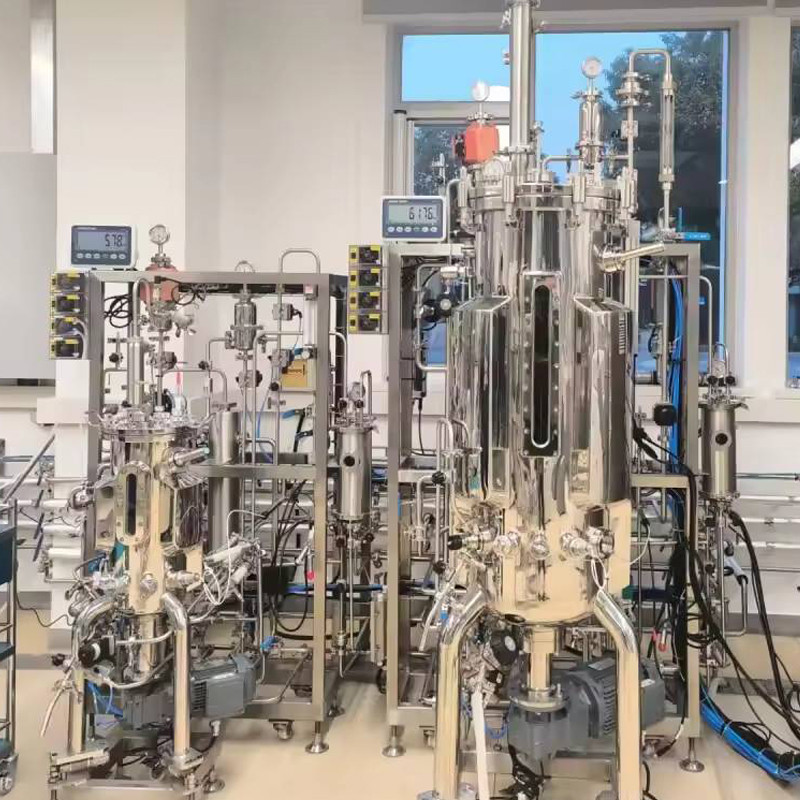
The control systems in industrial fermenters are also significantly more complex than those in the laboratory. Sophisticated sensors and automated feedback mechanisms are used to monitor and adjust multiple parameters in real-time. This ensures that the process remains within the optimal range, maximizing productivity and product quality.
Another important consideration in industrial fermenters is the issue of sterilization. Maintaining a sterile environment is essential to prevent contamination by unwanted microorganisms, which could have detrimental effects on the fermentation process and the final product. Industrial-scale sterilization methods, such as steam sterilization and the use of sterile filtration systems, are employed to ensure the integrity of the process.
The choice of the type of industrial fermenter or bioreactor depends on several factors, including the nature of the organism or cells being cultivated, the product being produced, and the specific requirements of the process. Batch fermenters are commonly used when a discrete quantity of product is desired, while continuous fermenters offer the advantage of a more consistent output over time.
In addition to traditional stirred-tank fermenters, other types of bioreactors have emerged in recent years. Membrane bioreactors, for example, use semi-permeable membranes to separate and retain cells or products, allowing for more efficient separation and purification processes. Immobilized cell bioreactors provide a means to anchor cells in a fixed matrix, enabling long-term operation and reduced cell washout.
The successful operation of industrial Parallel fermenters requires a multidisciplinary approach involving microbiology, engineering, chemistry, and computer science. Teams of experts work together to optimize the process, troubleshoot issues, and ensure the efficient and safe production of the desired products.
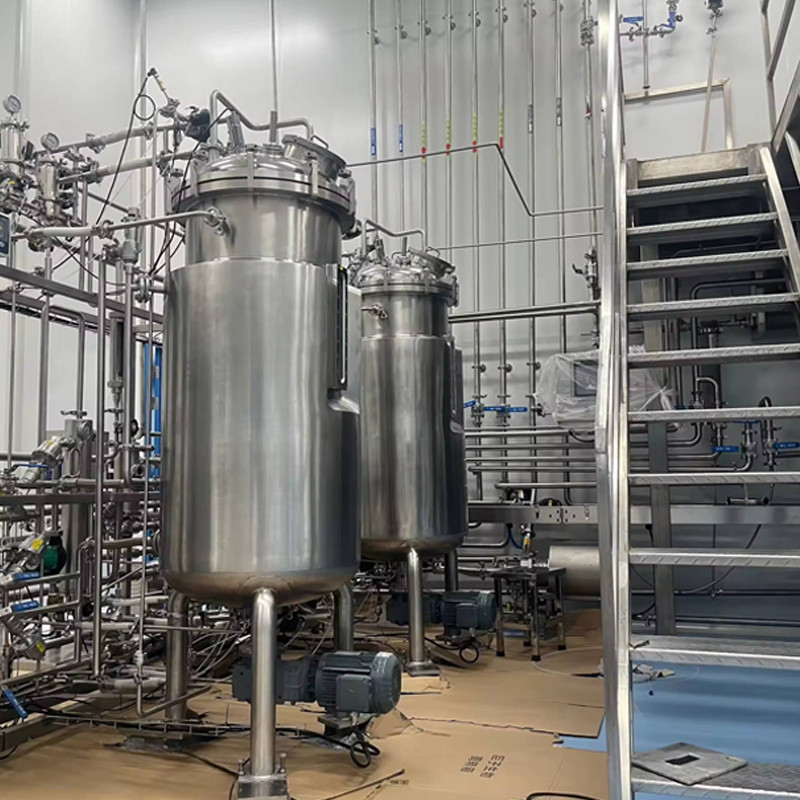
Looking to the future, the field of industrial fermenters and bioreactors is likely to witness further advancements. Developments in materials science will lead to the creation of more durable and biocompatible reactor materials. Advances in sensor technology and artificial intelligence will enable even more precise control and predictive maintenance of the systems. Moreover, the growing focus on sustainability will drive the development of more energy-efficient and environmentally friendly fermentation processes.
In conclusion, industrial fermenters and bioreactors are at the heart of modern industrial biotechnology. The seamless transition from laboratory-scale fermentation tanks to large-scale industrial production facilities is a complex but essential journey that requires continuous innovation and collaboration across multiple disciplines. By understanding and harnessing the power of these systems, we can continue to drive progress in the production of essential products for various industries, from pharmaceuticals and food to biofuels and chemicals.