200L Industrial Batch Fermentation Bioreactor for Microbiology: Unleashing Potential and Driving Innovation
In the dynamic realm of microbiology and industrial processes, the 200L industrial batch fermentation bioreactor has emerged as a vital tool, playing a crucial role in the production of various microbial-based products and driving advancements in multiple sectors. This article aims to provide an in-depth examination of this significant piece of equipment, exploring its design, functionality, applications, and the challenges and opportunities it presents.
The design of the 200L industrial batch fermentation bioreactor is a meticulous combination of engineering principles and microbiological requirements. The reactor vessel is typically constructed from materials that offer durability, chemical resistance, and sterilization capabilities. Stainless steel is often the preferred choice due to its robustness and ability to withstand the harsh conditions of fermentation processes.
The internal components of the bioreactor are designed to ensure optimal conditions for microbial growth and metabolite production. Agitation systems, such as impellers or magnetic stirrers, are incorporated to ensure uniform mixing of the culture medium, facilitating the distribution of nutrients, oxygen, and heat throughout the vessel.
Temperature control is achieved through jackets or coils that allow for the circulation of heating or cooling fluids, enabling precise maintenance of the desired temperature range.
Oxygen supply is a critical aspect, especially for aerobic microbial processes. Aeration systems, including spargers or membrane oxygenators, are employed to introduce an adequate amount of oxygen, ensuring the metabolic needs of the microorganisms are met. The design also considers the prevention of excessive foaming, which can negatively impact the process.
The functionality of the 200L industrial batch fermentation bioreactor lies in its ability to create a controlled and monitored environment for microbial cultures. Sensors are installed to continuously measure and monitor parameters such as pH, dissolved oxygen levels, cell density, and metabolite concentrations. This real-time data is crucial for making informed decisions and adjustments during the fermentation process to optimize productivity and product quality.
One of the key applications of this bioreactor is in the production of antibiotics and other pharmaceutical compounds. Microorganisms are cultivated under controlled conditions to produce the desired therapeutic substances with high purity and potency. The bioreactor's precise control over the process parameters helps ensure consistency and reliability in the production of these life-saving drugs.
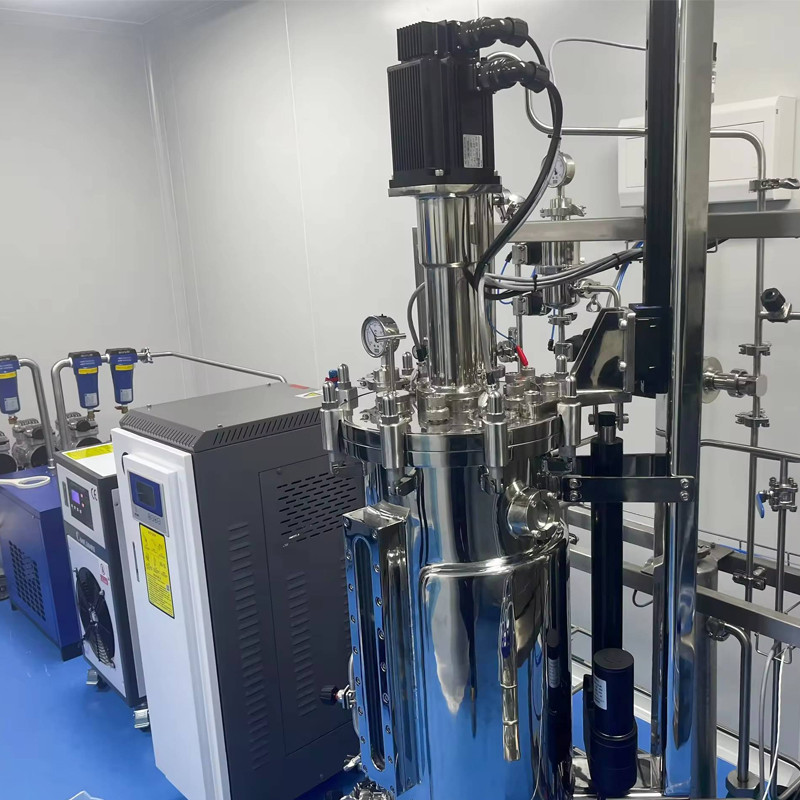
In the food and beverage industry, it is utilized for the production of enzymes, organic acids, and flavor compounds. The controlled fermentation environment allows for the development of products with specific characteristics and quality attributes, meeting the demanding standards of the market.
The bioreactor also finds application in the field of environmental microbiology, where microorganisms are used for bioremediation processes to degrade pollutants and contaminants. The ability to scale up the process in a 200L reactor provides a practical solution for treating larger volumes of contaminated materials.
However, the operation of a 200L industrial batch fermentation bioreactor is not without challenges. Maintaining sterility throughout the process is of paramount importance to prevent contamination, which can lead to batch failure and significant economic losses. The validation and optimization of the sterilization procedures are essential to ensure a contamination-free environment.
The scalability of the process from laboratory-scale to the 200L industrial scale can pose difficulties. Changes in fluid dynamics, mass transfer, and heat transfer can affect the performance of the fermentation. Thorough process development and scale-up studies are necessary to address these issues and ensure the success of the industrial-scale operation.
The selection and optimization of the culture medium and the strain of microorganisms are also critical factors that can significantly impact the productivity and efficiency of the fermentation process. Ongoing research and development efforts are focused on identifying novel and cost-effective medium components and improving the performance of microbial strains through genetic engineering or adaptive evolution.
Despite these challenges, the 200L industrial batch Industrial Microbiology fermentation bioreactor offers numerous opportunities for innovation and improvement. The integration of advanced process control strategies, such as model predictive control and artificial intelligence-based algorithms, can further enhance the performance and optimization of the fermentation process.
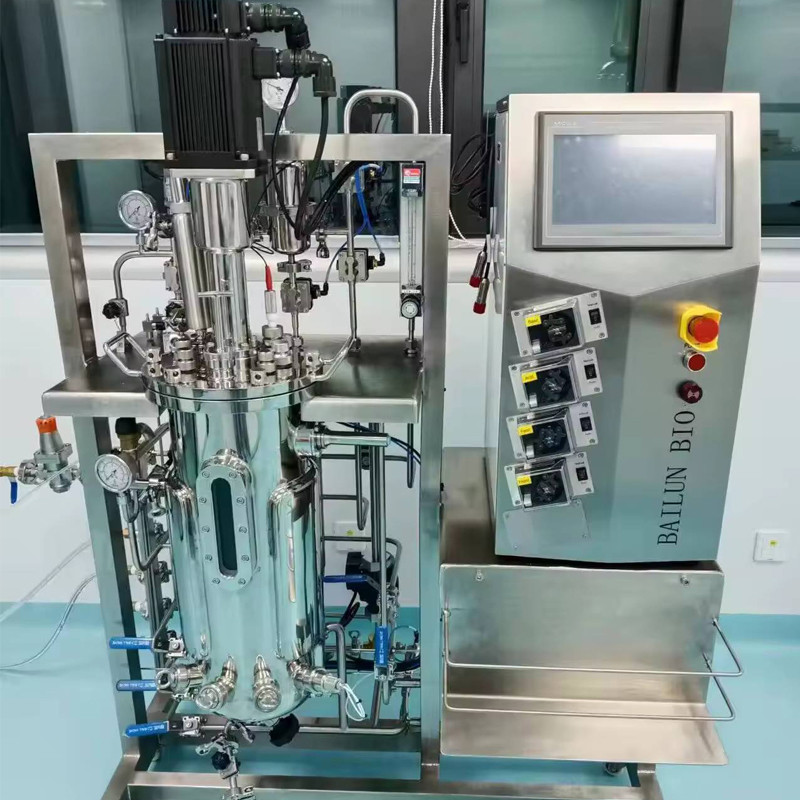
The development of new sensor technologies that provide more accurate and real-time measurements of key parameters can lead to better decision-making and process control. Additionally, the exploration of novel microbial strains and metabolic pathways holds the potential for the production of new and valuable compounds.
In conclusion, the 200L industrial batch fermentation bioreactor for microbiology is a powerful tool that has revolutionized the industrial production of microbial-based products. Its ability to provide a controlled and scalable environment for microbial growth and metabolism makes it indispensable in various industries.
Continued research and development in this field will undoubtedly lead to further enhancements in its performance, opening up new avenues for the production of innovative and sustainable microbial-based products that have a significant impact on our lives and the environment.