Home / All / Knowledge sharing /
Insights into the 200L Industrial Batch Fermentation Bioreactor for Microbiology
Categories
- Lab fermenter(SS316, 5L-50L)
- Industrial Fermenter Bioreactor Antibiotic Stainless Steel Bioreactor Laboratory Fermentation Tank
- Fermentor Cell Culture Bioreator Laboratory Fermenter Bioreactor Fermentation Bioreactor
- Bioreactor Cell Microbial Culture Biofermentation Tank
- Bioreactor Bioreactor Fermenter Bioreactor Fermentor
- Small Scale Methanol Plant For Laboratory Multi Bioreactor Pressure Fermentation
- International Technology Cell Culture Bioreactor
- Benchtop Multiple Bioreactor-MINI International Technology Cell Culture Bioreactor
- Airlift Bioreactor Fermentor Cell Culture Bioreator Laboratory Fermenter Bioreactor Fermentation Bioreactor
- Stainless Steel Bioreactor Customize Fermenter bioreactor industrial Fermentor
- Industrial Fermenter Bioreactor Industrial Fermenter Laboratory Fermentation Tank
- A Small Fermentation Tank Fermentation Equipment Stirred By A Biological Fermentation Tank
- Stainless steel Cell Culture Fermenter Fermentor Bioreactor
- Cell Culture Fermentation Tank microorganism Fermentation Tank 60l Stainless Tank Fermenter
- Stainless Steel Multiple-Step Fermentor Bioreactor Bioreactor Fermenter Bioreactor Fermentor
- Stainless Steel Solid Fermentor Cell Culture Parallel Multiple Bioreactor
- Stainless Steel Parallel Bioreactor Fermentation Bioreactor
- Single-Use Bioreactor Stainless Steel Mechanical Stirring Bioreactor bioreactor Stirred Tank fermentation Process Fermenter
- Industrial Fermenter Bioreactor Antibiotic Stainless Steel Bioreactor Laboratory Fermentation Tank
- Industry fermenter(1KL-400KL)
- CIP station
- Lab glass fermenter 2L-40L
- CIP station Laboratory Bioreactor cell Culture Bioreactor Bioreactor
- Stainless Steel Fermenter Bioreactor Industrial Fermenter Bioreactor Plant Cell Cultivation Bioreactor
- 200l Industrial Batch Fermentation Bioreactor For Microbiology
- Bioreactor Batch Fermentation Bioreactor For Microbiology
- Stainless Steel For Microorganism Cultivation Bioreactor
- Steam Generator Pharma Manufacturing Bioreactor bioreactor Perfusion System 200 Liter Stainless Conical Fermenter
- Spray Dryer Fermentor Cell Culture Bioreator Laboratory Fermenter Bioreactor Fermentation Bioreactor
- Mammalian cell bioreactor(5L-10KL)
- Lab Fermenter Bioreactor Industrial Stainless Steel Fermenter
- Vaccine Fermenter(GMP) Fermentation Equipment stainless Steel Bioreactor
- Mini Lab Glass Fermenter Magnetic Mixing Cell Culture Fermenter Bioreactor
- CIP Station Automatic Bioreactor Fermenter
Insights into the 200L Industrial Batch Fermentation Bioreactor for Microbiology
Question 1: What is the main purpose of a 200L industrial batch fermentation bioreactor in microbiology?
The 200L industrial batch fermentation bioreactor is designed to provide a controlled environment for the growth and metabolism of microorganisms on a relatively large scale. It enables the production of microbial metabolites, enzymes, or other valuable products in an efficient and reproducible manner.
Question 2: How is the temperature controlled within the bioreactor?
The bioreactor is equipped with a heating and cooling system. This could involve jackets around the vessel through which heated or cooled fluids are circulated, or internal coils. Sensors monitor the temperature, and a control system adjusts the flow of the fluids or the activation of heating/cooling elements to maintain the desired temperature.
Question 3: What types of microorganisms can be cultivated in this size of bioreactor?
A wide range of microorganisms can be grown, including bacteria, yeast, fungi, and some types of algae. The choice depends on the specific application and the requirements of the production process.
Question 4: How is the oxygen supply managed for aerobic microorganisms?
Oxygen is typically supplied through aeration systems such as spargers that introduce air or oxygen gas into the liquid medium. The rate and size of the bubbles, as well as the agitation speed, are adjusted to ensure adequate oxygen transfer without causing excessive shear stress on the cells.
Question 5: What role does pH play in the fermentation process and how is it maintained?
pH is critical as it affects the enzymatic activity and growth of microorganisms. pH sensors monitor the medium's pH, and when it deviates from the optimal range, acids or bases are added automatically to bring it back to the desired level.
Question 6: How is the sterility of the bioreactor Industrial ensured?
Sterility is maintained through a combination of rigorous cleaning and sterilization procedures before and after each batch. The bioreactor is designed to prevent the entry of contaminants during the fermentation process, with sealed ports and proper filtration of incoming gases and liquids.
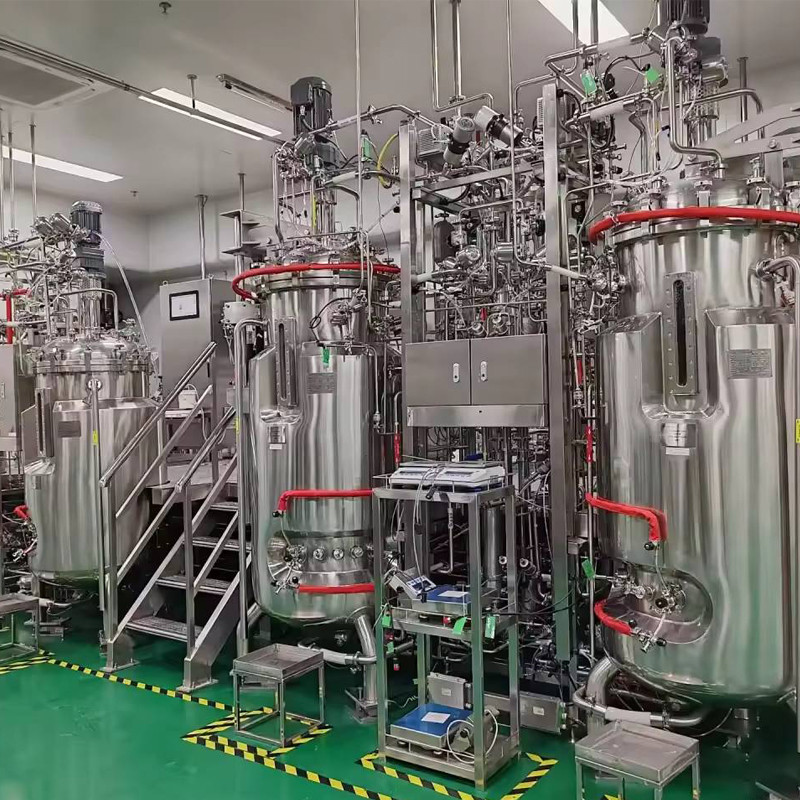
Question 7: Can this bioreactor be used for both research and industrial production?
Yes, it can be utilized in both settings. In research, it allows for larger-scale experiments to optimize processes before scaling up to full industrial production. In industrial applications, it can be part of a manufacturing line to produce significant quantities of the desired product.
Question 8: How is the mixing of the contents within the bioreactor achieved?
Mixing is usually accomplished through mechanical agitation, such as the rotation of impellers or stirrers. The design and speed of the agitation system are selected to ensure uniform distribution of nutrients, oxygen, and heat throughout the vessel.
Question 9: What kind of monitoring and control systems are typically incorporated in the 100l bioreactor?
Common monitoring systems include sensors for temperature, pH, dissolved oxygen, cell density, and substrate concentration. The control systems adjust parameters like aeration rate, agitation speed, nutrient addition, and pH adjustment based on the data collected from these sensors.
Question 10: What are the challenges in operating a 200L industrial batch fermentation bioreactor?
Some challenges include maintaining consistent process conditions, preventing contamination, optimizing the fermentation parameters for different microbial strains, and dealing with the complexity of the equipment and control systems. Additionally, efficient cleaning and sterilization can be time-consuming and energy-intensive.
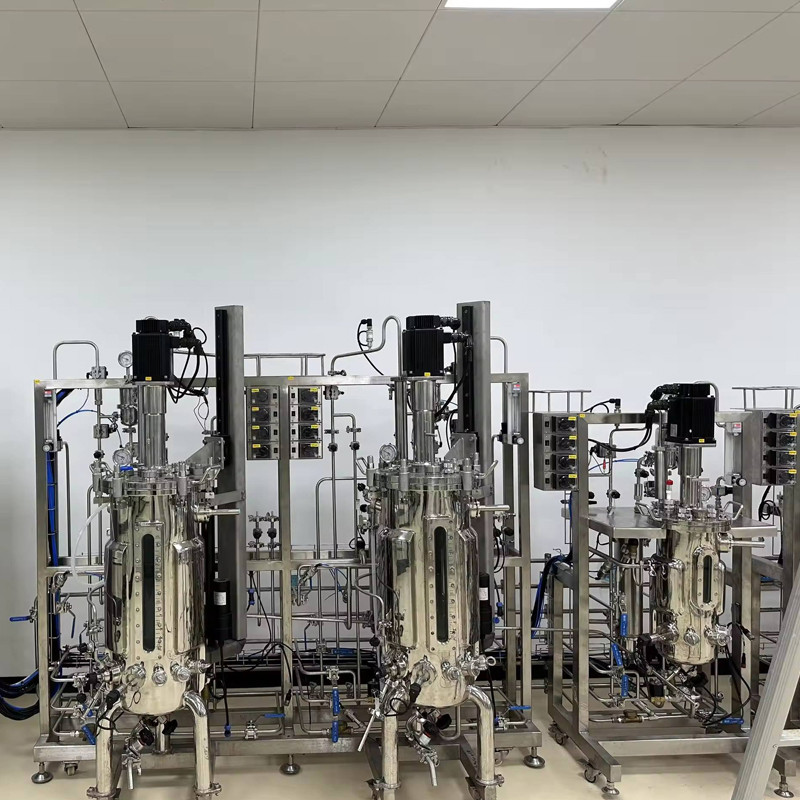
Navigation
Categories
- Lab fermenter(SS316, 5L-50L)
- Industrial Fermenter Bioreactor Antibiotic Stainless Steel Bioreactor Laboratory Fermentation Tank
- Fermentor Cell Culture Bioreator Laboratory Fermenter Bioreactor Fermentation Bioreactor
- Bioreactor Cell Microbial Culture Biofermentation Tank
- Bioreactor Bioreactor Fermenter Bioreactor Fermentor
- Small Scale Methanol Plant For Laboratory Multi Bioreactor Pressure Fermentation
- International Technology Cell Culture Bioreactor
- Benchtop Multiple Bioreactor-MINI International Technology Cell Culture Bioreactor
- Airlift Bioreactor Fermentor Cell Culture Bioreator Laboratory Fermenter Bioreactor Fermentation Bioreactor
- Stainless Steel Bioreactor Customize Fermenter bioreactor industrial Fermentor
- Industrial Fermenter Bioreactor Industrial Fermenter Laboratory Fermentation Tank
- A Small Fermentation Tank Fermentation Equipment Stirred By A Biological Fermentation Tank
- Stainless steel Cell Culture Fermenter Fermentor Bioreactor
- Cell Culture Fermentation Tank microorganism Fermentation Tank 60l Stainless Tank Fermenter
- Stainless Steel Multiple-Step Fermentor Bioreactor Bioreactor Fermenter Bioreactor Fermentor
- Stainless Steel Solid Fermentor Cell Culture Parallel Multiple Bioreactor
- Stainless Steel Parallel Bioreactor Fermentation Bioreactor
- Single-Use Bioreactor Stainless Steel Mechanical Stirring Bioreactor bioreactor Stirred Tank fermentation Process Fermenter
- Industrial Fermenter Bioreactor Antibiotic Stainless Steel Bioreactor Laboratory Fermentation Tank
- Industry fermenter(1KL-400KL)
- CIP station
- Lab glass fermenter 2L-40L
- CIP station Laboratory Bioreactor cell Culture Bioreactor Bioreactor
- Stainless Steel Fermenter Bioreactor Industrial Fermenter Bioreactor Plant Cell Cultivation Bioreactor
- 200l Industrial Batch Fermentation Bioreactor For Microbiology
- Bioreactor Batch Fermentation Bioreactor For Microbiology
- Stainless Steel For Microorganism Cultivation Bioreactor
- Steam Generator Pharma Manufacturing Bioreactor bioreactor Perfusion System 200 Liter Stainless Conical Fermenter
- Spray Dryer Fermentor Cell Culture Bioreator Laboratory Fermenter Bioreactor Fermentation Bioreactor
- Mammalian cell bioreactor(5L-10KL)
- Lab Fermenter Bioreactor Industrial Stainless Steel Fermenter
- Vaccine Fermenter(GMP) Fermentation Equipment stainless Steel Bioreactor
- Mini Lab Glass Fermenter Magnetic Mixing Cell Culture Fermenter Bioreactor
- CIP Station Automatic Bioreactor Fermenter
News
- Synthetic biology disrupts the anti-aging industry! Due to a 90% drop in cost, the market for ergot sulfur is expected to exceed 100 billion yuan by 2026!Jul 4,2025Ergothionine (EGT) is a natural sulfur-containing amino acid and currently the only known natural 2-thioimidazole amino acid.
- Production rate of 200%! The eight directions of "AI+fermentation" include multimodal fusion, multi temporal prediction, millisecond level control, and digital twins ..Jul 3,2025In the future, we need to promote the shift of biomanufacturing from experience driven to data-driven through the closed-loop technology of "data collection regulation optimization deployment".