Home / All / Knowledge sharing /
Insights into the Automatic Fermenter Bioreactor 100L for Bacteria Cultivation
Insights into the Automatic Fermenter Bioreactor 100L for Bacteria Cultivation
Question 1: What is the main purpose of an Automatic Fermenter Bioreactor 100L?
The main purpose is to provide a controlled and optimized environment for the growth and metabolism of bacteria on a relatively large scale (100L) with automated processes for enhanced efficiency and reproducibility.
Question 2: How does the 100L capacity of the bioreactor affect its performance and applications?
The 100L capacity offers a balance between providing sufficient volume for meaningful production and manageable operation. It is suitable for mid-scale experiments, pilot studies, and small-scale commercial production. It allows for more significant sample collection and analysis while still being feasible to control and monitor compared to much larger systems.
Question 3: What types of bacteria can be cultivated in this bioreactor?
A wide range of bacteria can be cultivated, including but not limited to industrial microorganisms used in the production of antibiotics, enzymes, and biofuels, as well as probiotic bacteria and those used in environmental remediation.
Question 4: How is the temperature controlled within the bioreactor?
The bioreactor is equipped with a temperature control system that may include heating elements and cooling mechanisms. Sensors monitor the internal temperature, and the control unit adjusts the heating or cooling to maintain the desired setpoint.
Question 5: What role does pH play in the fermentation process and how is it managed in the bioreactor?
pH is critical as it affects the enzymatic activity and metabolic pathways of the bacteria. The bioreactor has pH sensors and mechanisms for adding acids or bases to maintain the pH within the optimal range for the specific bacteria and process.
Question 6: How is oxygen supply regulated for aerobic bacteria in the 100L bioreactor?
Specialized aeration systems, such as spargers or membrane oxygenators, are used. The rate of oxygen supply is controlled based on the oxygen demand of the bacteria, which is monitored and adjusted automatically.
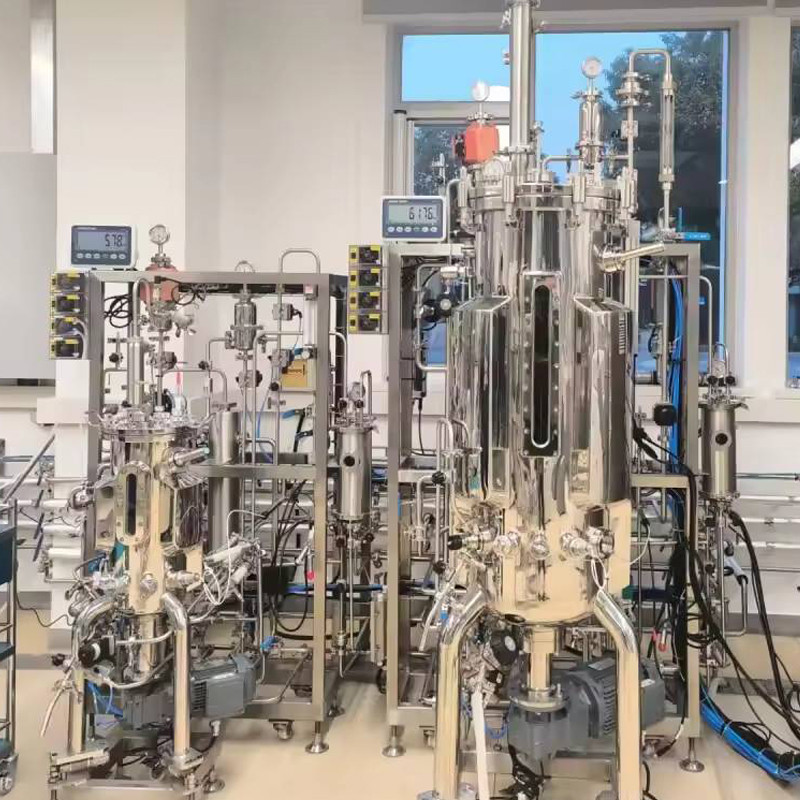
Question 7: What kind of agitation or mixing systems are typically employed in this size of bioreactor?
Commonly, impellers or stirrers of various designs are used. The choice depends on factors like the viscosity of the medium and the specific requirements of the bacterial culture to ensure uniform mixing and distribution of nutrients.
Question 8: How is sterility maintained in the Automatic Fermenter Bioreactor 100L?
Sterility is maintained through rigorous cleaning and sterilization procedures before and after each use. The bioreactor is designed with features to prevent contamination, such as sealed ports and sterilizable components.
Question 9: Can the bioreactor be used for continuous or batch fermentation processes?
Both continuous and batch fermentation processes can be carried out depending on the specific requirements of the experiment or production. The control systems can be configured accordingly.
Question 10: What kind of data and analytics can be obtained from the bioreactor for process optimization?
Data such as cell growth kinetics, substrate consumption, product formation rates, and changes in various parameters over time can be collected. This data is analyzed to optimize the fermentation process, identify potential bottlenecks, and make informed decisions for improved productivity and quality.
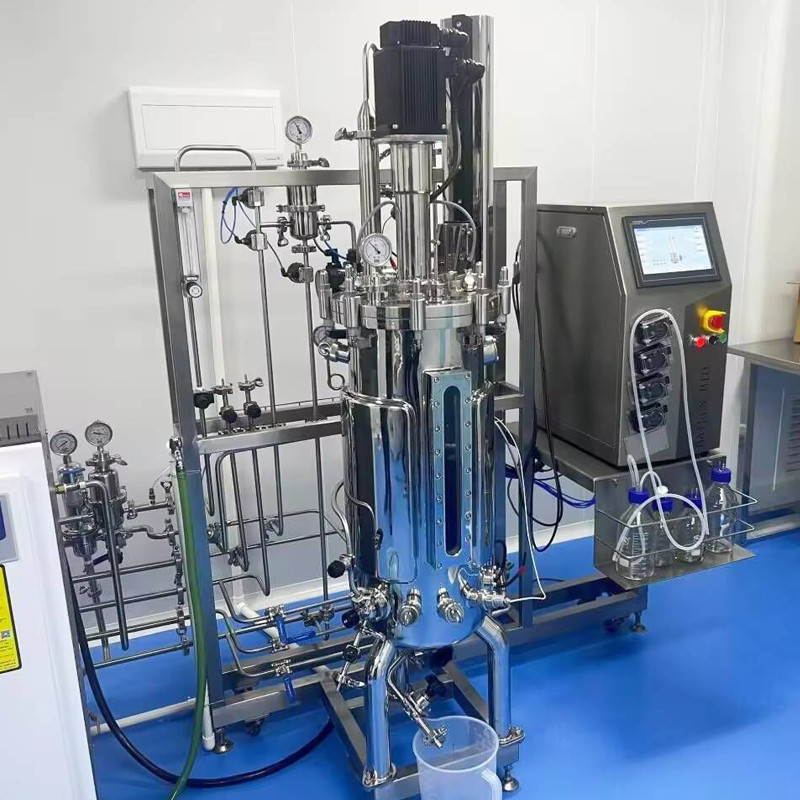
Navigation
News
- A Technological Marvel in BiotechnologyJun 24,2024Cell Culture Bioreactor Stainless Steel Fermenter Culture Machine: A Technological Marvel in Biotechnology
- The Backbone of Modern BioprocessingJun 24,2024Fermentation Equipment stainless Steel Bioreactor: The Backbone of Modern Bioprocessing