Home / All / Knowledge sharing /
Insights into Industrial Fermenter Bioreactors and Laboratory Fermentation Tanks
Insights into Industrial Fermenter Bioreactors and Laboratory Fermentation Tanks
Question 1: What is the main difference between an Industrial Fermenter Bioreactor and a Laboratory Fermentation Tank?
The main differences lie in their size, capacity, and the purpose they serve. Industrial Fermenter Bioreactors are large-scale systems designed for mass production of substances, often in commercial settings. They have a much higher capacity and are built to handle large volumes of raw materials and products. Laboratory Fermentation Tanks, on the other hand, are smaller and are used for research, experimentation, and process development.
Question 2: How is the scalability of processes managed from a Laboratory Fermentation Tank to an Industrial Fermenter Bioreactor?
Scalability involves careful consideration of various factors. Parameters such as mixing efficiency, heat transfer, oxygen supply, and nutrient distribution need to be adjusted when moving from the laboratory scale to the industrial scale. Mathematical models and pilot-scale studies are often employed to predict and optimize the performance of the industrial bioreactor based on the data obtained from the laboratory tank.
Question 3: What types of industries commonly use Industrial Fermenter Bioreactors?
Industries such as pharmaceuticals, food and beverage, biofuels, and wastewater treatment frequently utilize Industrial Fermenter Bioreactors. In the pharmaceutical industry, they are used for the production of antibiotics and vaccines. The food and beverage sector uses them for the manufacture of beverages and food additives. Biofuel production relies on them for converting biomass into usable fuel, and in wastewater treatment, they aid in the breakdown of organic matter.
Question 4: What safety features are typically incorporated in an Industrial Fermenter Bioreactor?
Safety features may include pressure relief valves to prevent over-pressurization, temperature sensors with automatic shut-off in case of overheating, and leak detection systems. Additionally, explosion-proof electrical components and emergency stop buttons are common to ensure the safety of operators and the surrounding environment.
Question 5: How is the quality control maintained in an Industrial Fermenter Bioreactor?
Quality control is maintained through continuous monitoring of process parameters such as pH, dissolved oxygen, temperature, and cell growth. Regular sampling and analysis of the product are also conducted to ensure it meets the required standards. Sophisticated control systems and data analytics help in identifying any deviations from the desired quality and taking corrective actions promptly.
Question 6: Can a Laboratory Fermentation Tank be used to simulate the conditions of an Industrial Fermenter Bioreactor accurately?
While a Laboratory Fermentation Tank can provide valuable insights and initial data, it cannot fully replicate the exact conditions of an industrial-scale bioreactor. However, with proper design and calibration, it can offer a close approximation and serve as a basis for scaling up the process.
Question 7: What are the common challenges faced when operating an Industrial Fermenter Bioreactor?
Some common challenges include maintaining sterility to prevent contamination, ensuring consistent and uniform mixing throughout the large volume, managing energy consumption for efficient operation, and dealing with unexpected mechanical or electrical failures. Also, optimizing the fermentation process to achieve maximum productivity and product quality is an ongoing challenge.
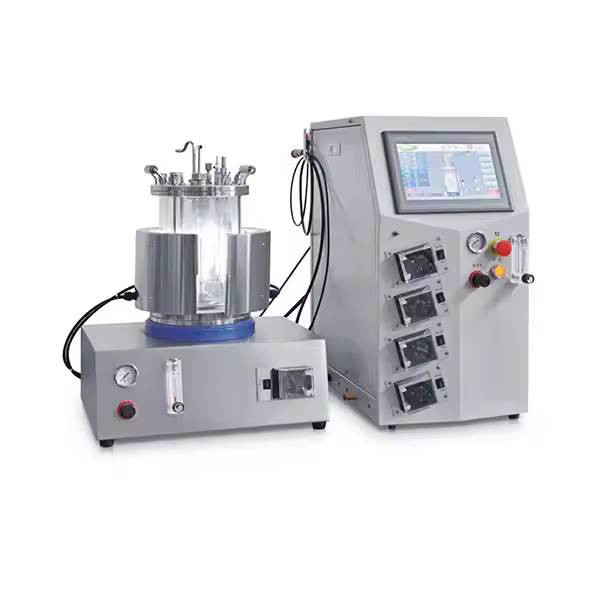
Question 8: How often does an Industrial Fermenter Bioreactor need to be serviced and maintained?
The frequency of servicing and maintenance depends on the usage, the nature of the process, and the manufacturer's recommendations. Generally, routine inspections, cleaning, and component replacements are carried out on a scheduled basis, which could range from monthly to annually.
Question 9: What materials are commonly used for the construction of Industrial Fermenter Cell Culture Bioreactors and Laboratory Fermentation Tanks?
Both are often made of stainless steel due to its corrosion resistance and ease of cleaning and sterilization. However, in some cases, special alloys or polymers may be used depending on the specific requirements of the process and the chemicals involved.
Question 10: How is the efficiency of oxygen transfer optimized in an Industrial Fermenter Bioreactor?
This can be achieved through various methods such as using efficient aeration systems, designing appropriate impellers for better mixing and gas dispersion, and controlling the agitation speed. Specialized oxygenation membranes or spargers may also be incorporated to enhance the oxygen transfer rate.
Question 11: What kind of control systems are used in Industrial Fermenter Bioreactors and Laboratory Fermentation Tanks?
Modern bioreactors and tanks typically employ computerized control systems that monitor and regulate parameters in real-time. These systems may include programmable logic controllers (PLCs) or distributed control systems (DCS) that allow for precise control and data logging.
Question 12: How is the cleaning and sterilization of an Industrial Fermenter Bioreactor different from a Laboratory Fermentation Tank?
The cleaning and sterilization processes are more complex and time-consuming for industrial bioreactors due to their larger size and higher production demands. Steam sterilization, chemical disinfectants, and CIP (Clean-In-Place) systems are commonly used. Laboratory tanks may have simpler sterilization methods such as autoclaving or using smaller-scale chemical sterilants.
Question 13: Can an Industrial Fermenter Bioreactor be retrofitted with new technologies or components to improve performance?
Yes, in many cases, bioreactors can be retrofitted with updated sensors, control systems, or improved mixing devices to enhance performance and meet changing production requirements. However, this needs to be done by qualified engineers and in accordance with safety and regulatory standards.
Question 14: How do environmental factors affect the operation of an Industrial Fermenter Bioreactor?
Environmental factors such as ambient temperature, humidity, and air quality can influence the performance of the cooling and ventilation systems of the bioreactor. Electrical fluctuations and water quality can also impact the operation of pumps, sensors, and control systems.
Question 15: What are the emerging trends in the design and operation of Industrial Fermenter Bioreactors and Laboratory Fermentation Tanks?
Emerging trends include the use of advanced materials for enhanced durability and biocompatibility, integration of artificial intelligence and machine learning for predictive maintenance and process optimization, and development of single-use bioreactors for increased flexibility and reduced cleaning validation efforts.
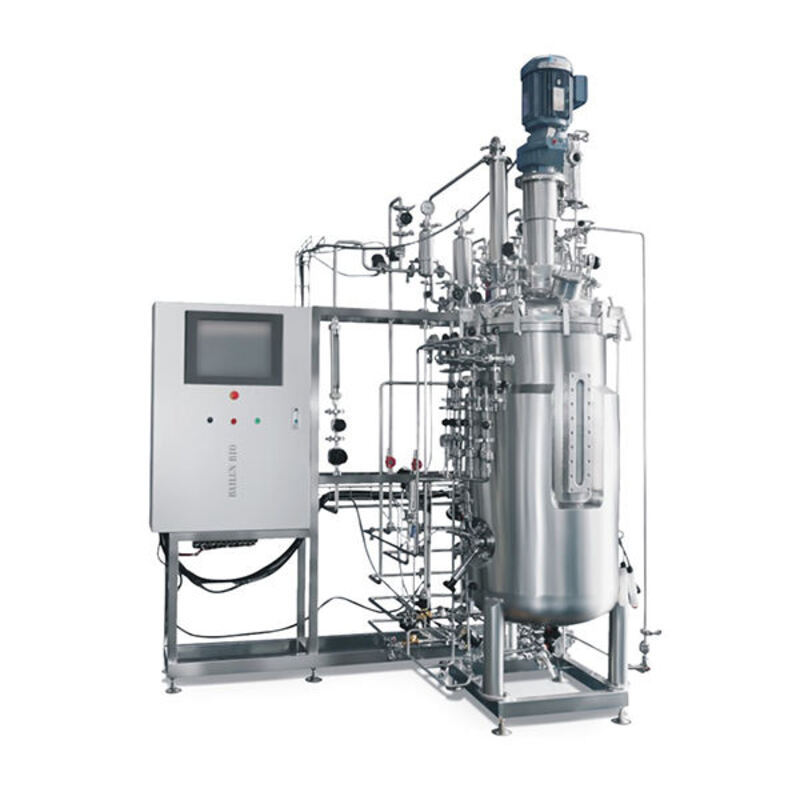
Navigation
News
- A Technological Marvel in BiotechnologyJun 24,2024Cell Culture Bioreactor Stainless Steel Fermenter Culture Machine: A Technological Marvel in Biotechnology
- The Backbone of Modern BioprocessingJun 24,2024Fermentation Equipment stainless Steel Bioreactor: The Backbone of Modern Bioprocessing