Small Scale Methanol Plant for Laboratory: Unveiling the Potential of Multi-Bioreactor Pressure Fermentation
In the realm of laboratory research and development, the establishment of a small scale methanol plant featuring multi-bioreactor pressure fermentation holds great significance and promise. This blog aims to delve deep into the various aspects of such a setup, exploring its design, functionality, applications, and the challenges it presents.
The concept of a small scale methanol plant for the laboratory is not only about miniaturization but also about precision and controlled experimentation. Such a facility is tailored to meet the specific needs of researchers who are exploring new frontiers in the field of methanol production and related bioprocesses.
At the heart of this setup are the multi-bioreactor pressure fermentation systems. These bioreactors are engineered to handle the complex biochemical reactions involved in methanol synthesis under pressurized conditions. The use of multiple bioreactors offers several advantages. It allows for parallel experiments, enabling researchers to compare and optimize different process parameters simultaneously. This parallelization speeds up the research process and provides a more comprehensive understanding of the factors influencing methanol production.
The pressurized environment in these bioreactors plays a crucial role. Pressure can affect various aspects of the Industrial fermentation process, including the solubility of gases, the kinetics of chemical reactions, and the activity of microorganisms or enzymes involved. By manipulating the pressure, researchers can study its impact on methanol yield and selectivity, uncovering optimal conditions for efficient production.
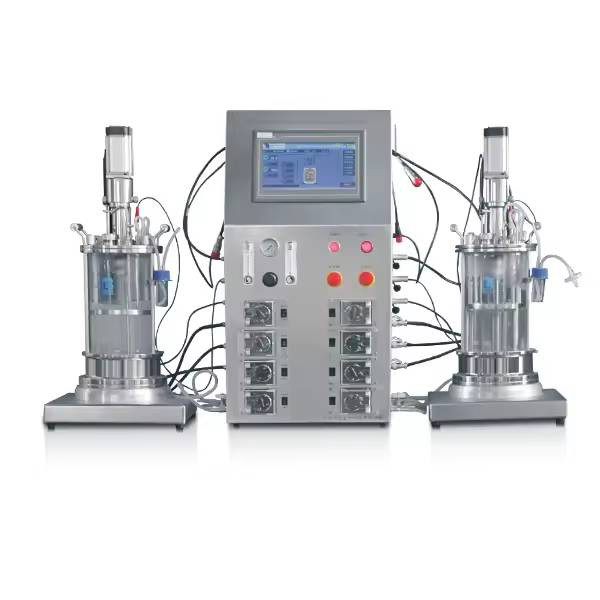
The design of these small-scale plants is a meticulous process that takes into account numerous factors. The size and configuration of the Cell Culture bioreactors are chosen to balance the need for sufficient sample volume with the constraints of laboratory space and resources. The materials used for construction must be resistant to the corrosive nature of the chemicals involved and capable of withstanding the applied pressure.
In terms of functionality, these plants are equipped with sophisticated monitoring and control systems. Sensors are installed to measure parameters such as temperature, pressure, pH, and substrate and product concentrations in real-time. This data is crucial for maintaining the desired conditions within the bioreactors and for making timely adjustments to ensure the success of the fermentation processes.
The application areas of a small scale methanol plant for the laboratory are diverse. It can be used to investigate novel catalysts and their performance in methanol synthesis. Researchers can test different combinations and formulations of catalysts to enhance the reaction rate and selectivity. This is crucial for developing more efficient and cost-effective production methods.
Another important application is the study of microbial consortia or engineered microorganisms for methanol production. By manipulating the genetic makeup of these organisms or optimizing their growth conditions within the bioreactors, it is possible to increase their productivity and efficiency.
Furthermore, these plants can be employed to explore the integration of different bioprocesses for a more sustainable methanol production. For example, coupling methanol synthesis with the utilization of waste materials or the capture and conversion of carbon dioxide could lead to greener and more environmentally friendly production strategies.
However, operating a small scale methanol plant for the laboratory comes with its fair share of challenges. Maintaining a sterile environment within the bioreactors is of paramount importance to prevent contamination, which could compromise the validity and reproducibility of the experiments. The pressure control systems need to be highly accurate and reliable to avoid any safety hazards and to ensure consistent experimental conditions.
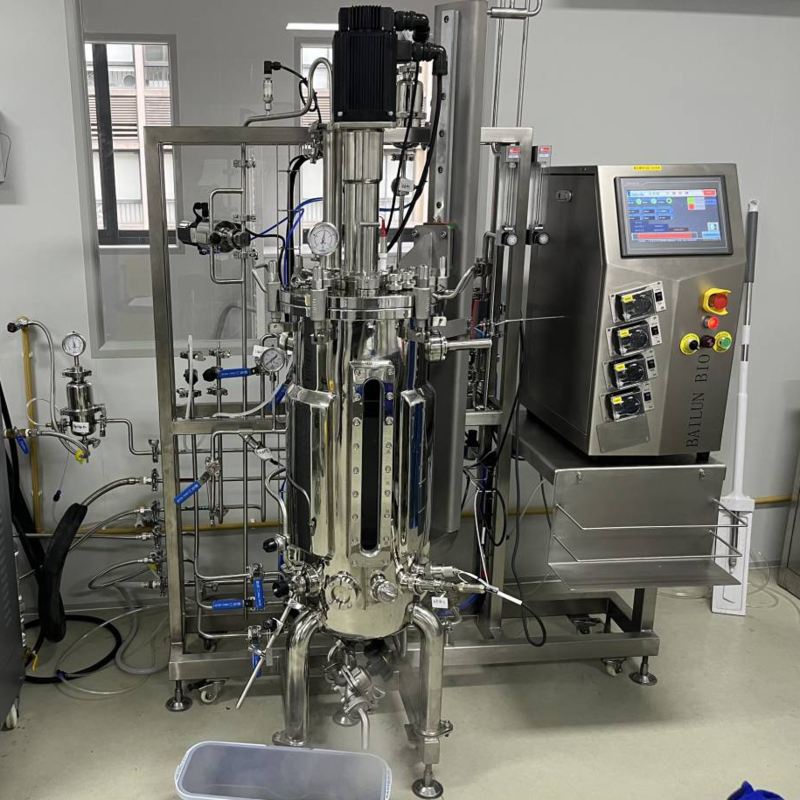
Calibration and maintenance of the monitoring equipment are also critical to ensure the accuracy and reliability of the data collected. Any errors or drifts in the sensor readings could lead to incorrect conclusions and wasted research efforts.
In addition, the complexity of the biochemical processes and the interaction of multiple variables make data interpretation and analysis a challenging task. Advanced statistical and modeling techniques are often required to extract meaningful insights from the large amounts of data generated during the experiments.
Despite these challenges, the potential benefits of a small scale methanol plant for the laboratory are immense. It provides a platform for cutting-edge research that can lead to significant advancements in methanol production technology. This could have far-reaching implications for various industries, including energy, chemicals, and materials.
Looking forward, continuous improvements and innovations in this field are expected. Advances in materials science could lead to the development of more durable and efficient 2000l bioreactor components. New sensor technologies might offer more precise and real-time monitoring capabilities. And the integration of artificial intelligence and machine learning in data analysis could accelerate the discovery of novel process optimizations.
In conclusion, a small scale methanol plant for the laboratory featuring multi-bioreactor pressure fermentation represents a powerful tool for researchers. It enables them to push the boundaries of knowledge and drive the development of more efficient, sustainable, and economically viable methods of methanol production. With ongoing efforts to overcome the challenges and embrace the opportunities, this area of research holds great promise for shaping the future of the energy and chemical industries.